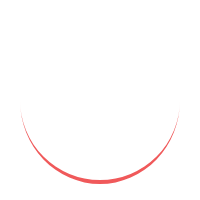
Quality control plays a crucial role in today's competitive business landscape. Whether it's manufacturing goods or providing services, maintaining high standards of quality is essential for success. A quality controller is an integral part of any organization that aims to deliver exceptional products or services consistently. In this article, we will explore the responsibilities, skills, and importance of quality controllers, along with the processes, tools, and challenges involved in quality control. So, let's dive in and discover the world of quality control.
IRole of a Quality Controller
As a quality controller, one is responsible for a range of tasks to maintain and improve the quality of products or services. These tasks may include inspecting raw materials, conducting in-process inspections, performing final product checks, and analyzing data to identify areas for improvement. The role also involves collaborating with other departments, such as production, engineering, and customer support, to address quality-related issues effectively. By conducting regular audits and implementing quality control measures, a quality controller ensures that products or services conform to established standards and meet customer expectations.
Skills and Qualifications
To be an effective quality controller, certain skills and qualifications are necessary. Technical knowledge and expertise in the specific industry are crucial for understanding the quality requirements and standards. Attention to detail is another vital skill, as quality controllers need to identify even the slightest deviations from the desired specifications. Strong problem-solving abilities are also essential for analyzing quality-related issues and implementing effective solutions. Additionally, communication skills are crucial for collaborating with cross-functional teams and conveying quality-related information to stakeholders.
Quality Control Processes
Quality control processes involve a series of steps to ensure that products or services meet the desired quality standards. These processes typically include inspection, testing, and documentation. Inspections can be carried out at various stages, such as incoming material inspection, in-process inspection, and final product inspection. Testing involves conducting specific tests to assess the product's functionality, performance, or other quality parameters. Documentation and record-keeping play a vital role in maintaining traceability and accountability, as they provide evidence of adherence to quality control procedures.
Quality Control Tools and Techniques
Various tools and techniques are employed in quality control to streamline processes and enhance product/service quality. Statistical process control (SPC) is a widely used method for monitoring and controlling quality during production. It involves collecting and analyzing data to identify any variations or abnormalities in the manufacturing process. Six Sigma and lean methodologies are also popular approaches that aim to reduce defects, minimize waste, and optimize efficiency. These tools and techniques empower quality controllers to make data-driven decisions and continuously improve quality.
Benefits of Quality Control
Implementing effective quality control practices brings numerous benefits to organizations. First and foremost, it ensures that products or services consistently meet or exceed customer expectations, resulting in improved customer satisfaction and loyalty. Quality control also helps prevent defects, reduce rework or rejection rates, and increase operational efficiency. By identifying and addressing quality issues early in the production process, organizations can save time, resources, and costs. Moreover, delivering high-quality products or services enhances brand reputation and competitiveness in the market.
Challenges in Quality Control
Quality control is not without its challenges. One of the major challenges is striking a balance between efficiency and quality. Organizations need to meet production targets and deadlines while ensuring that quality standards are not compromised. Additionally, keeping up with changing regulations and industry standards poses a continuous challenge for quality controllers. Adapting to new requirements and implementing necessary changes can be resource-intensive and time-consuming. However, organizations that successfully overcome these challenges are better positioned to maintain a competitive edge in the market.
Quality Control in Different Industries
Quality control is applicable across various industries. In the manufacturing sector, quality controllers play a crucial role in ensuring that products meet stringent quality standards. They monitor the production process, conduct inspections, and conduct tests to guarantee product integrity. In service-based industries such as healthcare or software development, quality controllers focus on maintaining high service quality and adhering to industry regulations. Regardless of the industry, quality control acts as a key driver for customer satisfaction and organizational success.
Future of Quality Control
The future of quality control lies in the integration of technology and automation. Advancements in artificial intelligence, machine learning, and data analytics offer exciting opportunities to streamline quality control processes and enhance accuracy. Automated inspection systems, real-time data analysis, and predictive analytics can enable early detection of quality issues and facilitate proactive decision-making. As organizations embrace digital transformation, quality controllers will play a pivotal role in leveraging technology to drive continuous improvement and achieve exceptional quality standards.
Quality Controller FAQs
1. What is the role of a quality controller?
A quality controller is responsible for overseeing the quality control processes in an organization. They ensure that products or services meet the established quality standards through inspections, testing, and analysis.
2. What are the essential skills for a quality controller?
Technical knowledge, attention to detail, problem-solving abilities, and effective communication skills are essential for a quality controller to excel in their role.
3. How does quality control benefit organizations?
Implementing quality control practices helps organizations deliver consistent high-quality products or services, enhance customer satisfaction, reduce defects and waste, and improve operational efficiency.
4. What are some challenges in quality control?
Balancing efficiency and quality, keeping up with changing regulations, and adapting to new requirements are some challenges faced in quality control.
5. What does the future hold for quality control?
The future of quality control lies in technology integration and automation, leveraging advancements in artificial intelligence, machine learning, and data analytics to enhance accuracy and drive continuous improvement.