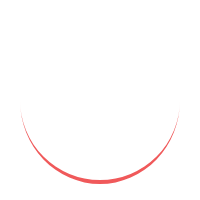
Manufacturing processes are the backbone of many industries, ensuring the production of high-quality goods efficiently. Behind the scenes, there is a dedicated professional who plays a crucial role in refining these processes, known as a Process Tryout Engineer. In this article, we will explore the responsibilities, skills, and impact of a Process Tryout Engineer, and how they contribute to enhancing manufacturing efficiency.
Introduction to the Role of a Process Tryout Engineer
The role of a Process Tryout Engineer is to optimize manufacturing processes by identifying and resolving inefficiencies, ensuring smooth operations, and maximizing productivity. They are responsible for conducting process tryouts, which involve testing, evaluating, and fine-tuning production processes to achieve optimal results.
Responsibilities and Key Tasks of a Process Tryout Engineer
As a Process Tryout Engineer, there are several responsibilities and tasks that one must undertake to achieve process optimization. These include:
Assessing process requirements: Understanding the specific requirements of the manufacturing process and identifying areas for improvement.
Designing tryout experiments: Developing and implementing tryout plans to test process modifications and evaluate their impact.
Data collection and analysis: Collecting relevant data during the tryout phase and analyzing it to identify trends, patterns, and areas of improvement.
Troubleshooting and problem-solving: Addressing issues and challenges that arise during the tryout phase, such as equipment malfunctions or process deviations.
Collaboration with cross-functional teams: Working closely with production engineers, quality assurance teams, and other stakeholders to ensure effective communication and collaboration for process enhancements.
Process documentation: Documenting the changes made during the tryout process, including procedures, best practices, and recommendations for future optimization.
Continuous improvement: Proactively seeking opportunities for process improvements, staying updated with industry trends, and implementing innovative solutions to enhance manufacturing efficiency.
Qualifications and Skills Required for the Role
To excel as a Process Tryout Engineer, certain qualifications and skills are essential. These include:
Technical knowledge: A strong foundation in engineering principles, manufacturing processes, and relevant technologies is crucial for understanding and optimizing production systems.
Analytical skills: The ability to collect and analyze data, identify patterns, and draw meaningful insights is vital for making data-driven decisions during the tryout phase.
Problem-solving abilities: Process Tryout Engineers should possess excellent problem-solving skills to tackle unforeseen challenges and develop effective solutions.
Communication and collaboration: Strong interpersonal skills are necessary to collaborate with cross-functional teams, convey complex ideas, and facilitate effective communication throughout the process tryout phase.
Attention to detail: Being meticulous and detail-oriented is important for identifying subtle inefficiencies in manufacturing processes and implementing precise modifications.
Adaptability and resilience: The ability to adapt to changing circumstances and overcome setbacks is crucial, as process tryouts often involve experimentation and iterative improvements.
Safety consciousness: Process Tryout Engineers must prioritize safety measures and adhere to relevant regulations to ensure a secure working environment for all personnel involved.
Understanding the Importance of Process Tryouts in Manufacturing
Process tryouts play a vital role in ensuring manufacturing efficiency. They help identify bottlenecks, eliminate waste, optimize resource utilization, and enhance product quality. By conducting thorough tryouts, manufacturers can refine their processes, streamline operations, and ultimately reduce costs while meeting customer demands.
The Process Tryout Engineer's Role in Optimizing Production Processes
Process Tryout Engineers are at the forefront of process optimization efforts. Their contributions are instrumental in enhancing production efficiency. By leveraging their expertise, they can:
Identify inefficiencies: Through data analysis and observation, Process Tryout Engineers can identify areas of inefficiency within manufacturing processes.
Implement modifications: By designing and executing tryout experiments, these engineers can introduce process modifications aimed at resolving identified inefficiencies.
Evaluate performance: Process Tryout Engineers assess the impact of modifications by collecting and analyzing data, enabling them to determine the effectiveness of the changes made.
Optimize processes: With the insights gained from tryouts, Process Tryout Engineers can fine-tune manufacturing processes to maximize efficiency, minimize waste, and improve overall productivity.
Steps Involved in Conducting a Process Tryout
The process tryout phase typically involves the following steps:
Define objectives: Clearly define the goals and objectives of the tryout, such as reducing cycle time, improving product quality, or optimizing resource usage.
Plan tryout experiments: Develop a comprehensive plan that outlines the specific modifications to be made, the data to be collected, and the evaluation criteria to be used.
Execute the tryout: Implement the planned modifications, monitor the process closely, and collect relevant data at each stage.
Analyze and interpret data: Analyze the collected data to identify trends, patterns, and areas for improvement. Interpret the results to draw meaningful insights.
Make adjustments: Based on the data analysis, make necessary adjustments to the process, equipment, or operating parameters to further enhance performance.
Evaluate outcomes: Assess the outcomes of the modifications made during the tryout phase, considering both qualitative and quantitative factors.
Document findings: Document the findings, including the changes made, the impact observed, and any recommendations for future process optimization.
Analyzing and Interpreting Data During the Tryout Phase
During the process tryout, the collection and analysis of data are critical for understanding the effectiveness of modifications. Process Tryout Engineers employ statistical tools, data visualization techniques, and analytical methods to gain insights from the collected data. This allows them to make informed decisions and optimize the manufacturing processes accordingly.
Troubleshooting and Problem-Solving During Process Tryouts
Process tryouts often encounter unexpected challenges and issues. Process Tryout Engineers must possess strong troubleshooting and problem-solving skills to address these hurdles effectively. They analyze the root causes of problems, devise solutions, and implement corrective actions to ensure a smooth and efficient tryout process.
Collaborating with Cross-Functional Teams for Process Improvements
Process Tryout Engineers work closely with various teams, including production engineers, quality assurance personnel, and operators, to achieve process improvements. Effective collaboration fosters a culture of continuous improvement, facilitates knowledge sharing, and ensures the successful implementation of process modifications.
Ensuring Safety and Compliance in the Tryout Phase
Safety and compliance are paramount during process tryouts. Process Tryout Engineers must prioritize the well-being of personnel involved and adhere to relevant safety protocols. Additionally, compliance with industry standards and regulations guarantees that the manufacturing processes meet quality and legal requirements.
The Impact of Process Tryouts on Product Quality and Customer Satisfaction
Process tryouts have a direct impact on product quality and customer satisfaction. By optimizing manufacturing processes, Process Tryout Engineers can enhance product consistency, reduce defects, and improve overall quality. This, in turn, leads to greater customer satisfaction, improved brand reputation, and increased customer loyalty.
Examples of Successful Process Tryouts and Their Outcomes
Several industries have witnessed the positive outcomes of successful process tryouts. For example:
Automotive manufacturing: Process Tryout Engineers in the automotive industry have improved production efficiency by fine-tuning assembly line processes, resulting in reduced cycle times and enhanced vehicle quality.
Electronics manufacturing: By conducting tryouts on circuit board production processes, engineers have identified and rectified inefficiencies, leading to improved product reliability and shorter time-to-market.
Pharmaceutical production: Process Tryout Engineers in pharmaceutical companies have optimized drug manufacturing processes, resulting in increased yields, reduced production costs, and improved compliance with regulatory standards.
Tools and Technologies Used by Process Tryout Engineers
Process Tryout Engineers leverage various tools and technologies to facilitate their work, including:
Data acquisition systems: These systems help in collecting real-time data during the tryout phase, enabling engineers to monitor and analyze process parameters effectively.
Statistical analysis software: Software tools like Minitab, JMP, or Excel's data analysis features assist in analyzing process data, identifying trends, and performing statistical calculations.
Process simulation software: Simulation tools like AutoCAD, SolidWorks, or Simul8 help engineers model and simulate different process scenarios, allowing them to predict outcomes and make informed decisions.
Quality management systems: Software platforms such as Six Sigma, Lean Manufacturing, or Total Quality Management systems aid in implementing standardized quality processes and monitoring performance metrics.
Continuous Learning and Professional Development for Process Tryout Engineers
To stay relevant in an ever-evolving manufacturing landscape, Process Tryout Engineers should embrace continuous learning and professional development. Engaging in training programs, attending industry conferences, and staying updated with the latest advancements ensures that they possess the necessary knowledge and skills to tackle emerging challenges and leverage new technologies.
Future Trends and Advancements in the Field of Process Tryouts
The field of process tryouts is expected to witness several advancements in the coming years. Some of the trends that Process Tryout Engineers should be aware of include:
Industry 4.0 integration: The integration of Internet of Things (IoT), artificial intelligence (AI), and big data analytics in manufacturing processes will revolutionize the way tryouts are conducted, enabling real-time monitoring, predictive maintenance, and autonomous decision-making.
Virtual and augmented reality: These technologies can simulate the tryout environment virtually, allowing engineers to visualize and analyze processes before implementing physical modifications, thereby reducing costs and improving efficiency.
Digital twin technology: Digital twins, virtual replicas of physical processes, provide engineers with a platform to test modifications and simulate the impact on the overall production system, facilitating more accurate tryouts.
Process Tryout Engineer FAQs
What is the difference between a Process Tryout Engineer and a Process Engineer?
A Process Tryout Engineer specializes in conducting tryouts, testing modifications, and evaluating process performance. A Process Engineer, on the other hand, focuses on designing and optimizing manufacturing processes as a whole.
What industries require the expertise of Process Tryout Engineers?
Process Tryout Engineers are employed in various industries, including automotive, electronics, pharmaceuticals, food and beverage, and heavy machinery manufacturing.
How long does a typical process tryout phase last?
The duration of a process tryout phase varies depending on the complexity of the process, the extent of modifications, and the desired outcomes. It can range from a few days to several weeks.
Can process tryouts be conducted remotely?
With advancements in technology, some aspects of process tryouts can be conducted remotely, especially when virtual simulations and remote monitoring systems are utilized. However, physical modifications often require on-site presence.
How can process tryouts contribute to sustainability efforts?
By optimizing manufacturing processes, reducing waste, and maximizing resource utilization, process tryouts can contribute to sustainability goals, such as energy conservation and minimizing environmental impact.