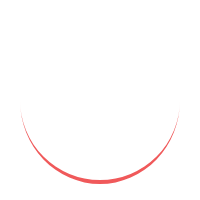
Plasma cutting is a versatile and efficient method of cutting through various types of metal. Whether you're a DIY enthusiast, a metal fabricator, or an artist, a plasma cutter can be a valuable addition to your toolbox. In this article, we will explore the ins and outs of plasma cutters, including their functionality, types, benefits, safety precautions, usage steps, maintenance, troubleshooting, applications, and tips for maximizing efficiency.
Introduction to Plasma Cutters
Plasma cutters are powerful tools that utilize an electrically conductive gas, known as plasma, to cut through metal. They provide a precise and controlled cutting process, making them popular in industries such as metal fabrication, automotive repair, and HVAC systems. Plasma cutters are capable of cutting through various metals, including steel, stainless steel, aluminum, and copper.
How Does a Plasma Cutter Work?
Plasma cutters work by passing an electric current through a gas, typically compressed air or nitrogen, which creates a high-temperature plasma arc. The plasma arc is directed through a small nozzle, where it becomes highly focused and reaches temperatures of up to 30,000 degrees Fahrenheit. This intense heat melts the metal, and a high-velocity jet of plasma blows away the molten metal, creating a clean and precise cut.
Types of Plasma Cutters
There are different types of plasma cutters available in the market, each suited for specific applications and requirements. Here are three common types:
Handheld Plasma Cutters
Handheld plasma cutters are portable and easy to maneuver. They are suitable for small-scale cutting tasks and offer excellent versatility. With a handheld plasma cutter, you can achieve intricate cuts, making it ideal for artistic metalwork and DIY projects.
CNC Plasma Cutters
CNC (Computer Numerical Control) plasma cutters are automated machines that follow pre-programmed cutting patterns. They are commonly used in large-scale industrial applications, where precision and speed are crucial. CNC plasma cutters are highly efficient and can cut through thick metal plates with ease.
Portable Plasma Cutters
Portable plasma cutters strike a balance between handheld and CNC models. They are compact and lightweight, making them convenient for on-site cutting tasks. Portable plasma cutters are favored by metalworkers who need mobility without compromising cutting power.
Benefits of Using a Plasma Cutter
Plasma cutters offer several advantages over traditional cutting methods. Here are some benefits:
Precision: Plasma cutters provide precise cuts, allowing for intricate designs and clean edges.
Speed: The high cutting speed of plasma cutters ensures efficiency and productivity.
Versatility: Plasma cutters can handle various metal thicknesses and types.
Ease of Use: With proper training and practice, plasma cutters are relatively easy to operate.
Minimal Heat Affected Zone: The focused plasma arc minimizes the heat-affected zone, reducing distortion and warping.
Portability: Handheld and portable plasma cutters offer flexibility and mobility.
Cost-effective: Plasma cutters can be cost-effective in the long run, considering their efficiency and reduced material wastage.
Factors to Consider When Buying a Plasma Cutter
When choosing a plasma cutter, it's essential to consider certain factors to ensure it meets your specific requirements. Here are some key considerations:
Cutting Capacity
The cutting capacity of a plasma cutter refers to the maximum thickness it can cut. Determine the thickness of the materials you'll be working with to select a cutter with adequate capacity.
Power Source
Plasma cutters can be powered by electricity or compressed air. Evaluate the power sources available in your workspace and choose a cutter accordingly.
Duty Cycle
The duty cycle indicates the amount of time a plasma cutter can operate continuously before requiring a cooling period. Consider the duty cycle to ensure it aligns with your workflow demands.
Cutting Speed
Different plasma cutters have varying cutting speeds. If you require fast and efficient cutting, opt for a cutter with a higher cutting speed.
Price
Consider your budget and the long-term value of the plasma cutter. While it's essential to find an affordable option, prioritize quality and durability.
Safety Precautions for Using a Plasma Cutter
Using a plasma cutter involves working with high temperatures and electrical currents, making safety precautions crucial. Here are some safety measures to follow:
Personal Protective Equipment (PPE)
Always wear appropriate PPE, including safety glasses, gloves, and protective clothing, to shield yourself from sparks, heat, and metal fragments.
Proper Ventilation
Ensure proper ventilation in the workspace to prevent the accumulation of fumes and gases generated during the cutting process.
Fire Safety Measures
Keep a fire extinguisher nearby and remove any flammable materials from the work area. Regularly inspect and maintain the plasma cutter to prevent potential fire hazards.
Steps to Use a Plasma Cutter
Using a plasma cutter requires proper setup and technique to achieve accurate and clean cuts. Follow these steps:
Preparing the Work Area
Clear the work area from clutter and flammable materials. Secure the metal piece to be cut in a stable position, ensuring it won't move during the cutting process.
Setting Up the Plasma Cutter
Connect the plasma cutter to the appropriate power source and ensure all connections are secure. Adjust the air pressure to the recommended level and attach the appropriate consumables to the torch.
Adjusting the Cutting Parameters
Set the cutting parameters based on the thickness and type of metal. This includes adjusting the amperage, gas flow rate, and torch height.
Cutting Techniques
Hold the torch perpendicular to the metal surface and maintain a steady cutting speed. Move the torch along the designated cutting path while maintaining a consistent arc length.
Post-Cutting Clean-up
After completing the cut, turn off the plasma cutter and allow the metal to cool down. Remove any slag or debris and clean the work area.
Maintenance and Care for Plasma Cutters
Regular maintenance and proper care will extend the lifespan of your plasma cutter and ensure optimal performance. Here are some maintenance tips:
Cleaning the Torch and Consumables
Clean the torch and replace consumables regularly to maintain cutting quality. Remove any spatter or debris that may accumulate on the torch nozzle and electrode.
Checking and Replacing Worn Parts
Inspect the plasma cutter regularly for worn or damaged parts. Replace any components that show signs of wear to avoid compromising cutting performance and safety.
Proper Storage
Store the plasma cutter in a dry and clean environment when not in use. Protect it from dust, moisture, and extreme temperatures.
Troubleshooting Common Issues with Plasma Cutters
While plasma cutters are reliable tools, occasional issues may arise. Here are some common problems and their solutions:
Poor Cutting Quality
If the cut edges are rough or uneven, ensure the consumables are in good condition and properly installed. Adjust the cutting parameters and torch height as needed.
Excessive Consumable Wear
If consumables wear out quickly, check for proper airflow and gas pressure. Ensure that the torch parts are clean and undamaged.
Electrical Problems
If the plasma cutter fails to start or experiences intermittent operation, check the power supply connections and ensure they are secure. If necessary, consult a professional for electrical troubleshooting.
Plasma Cutter vs. Other Cutting Tools
Plasma cutters offer several advantages over traditional cutting tools such as oxy-fuel cutting and mechanical saws. Compared to oxy-fuel cutting, plasma cutters are faster, more precise, and can cut a wider range of metals. When compared to mechanical saws, plasma cutters provide cleaner cuts and are more efficient for thick metal plates.
Applications of Plasma Cutters
Plasma cutters find applications in various industries. Here are a few examples:
Metal Fabrication
Plasma cutters are extensively used in metal fabrication for cutting and shaping metal components, such as brackets, frames, and panels.
Automotive Repair
Plasma cutters are valuable tools in the automotive industry for cutting and repairing exhaust systems, body panels, and suspension components.
HVAC Systems
Plasma cutters are utilized in HVAC systems to cut and shape ductwork, ensuring precise fittings and efficient airflow.
Artistic Metalwork
Plasma cutters are favored by artists and sculptors for creating intricate metal designs and sculptures.
Tips for Maximizing Efficiency and Accuracy with a Plasma Cutter
Here are some tips to help you make the most of your plasma cutter:
Practice: Familiarize yourself with the cutter's settings and techniques through practice cuts on scrap metal.
Secure the Metal: Use clamps or magnets to secure the metal piece firmly in place, minimizing movement during cutting.
Maintain Consistent Torch Height: Ensure the torch is held at a consistent height from the metal surface to achieve even and clean cuts.
Mark the Cutting Path: Use a guide or marking tool to indicate the desired cutting path, ensuring accuracy.
Clean the Consumables: Regularly clean the torch and replace worn consumables to maintain cutting quality and prolong their lifespan.
Plasma Cutter Manual FAQs
Q: Can I use a plasma cutter on any type of metal?
A: Plasma cutters can cut through various types of metals, including steel, stainless steel, aluminum, and copper. However, different plasma cutters may have specific recommendations for the types and thicknesses of metals they can cut effectively.
Q: How thick of a material can a plasma cutter cut?
A: The cutting capacity of a plasma cutter depends on its power and specifications. Generally, plasma cutters can cut metal plates ranging from a few millimeters to several inches thick.
Q: Is plasma cutting dangerous?
A: Plasma cutting involves high temperatures and electrical currents, making it potentially hazardous. However, by following proper safety precautions, wearing personal protective equipment, and adhering to recommended operating procedures, the risks can be minimized.
Q: What maintenance is required for a plasma cutter?
A: Regular maintenance for a plasma cutter includes cleaning the torch and consumables, checking for worn or damaged parts, and proper storage. Refer to the manufacturer's guidelines for specific maintenance procedures.
Q: Can I use a plasma cutter outdoors?
A: While plasma cutters can be used outdoors, it's crucial to ensure proper ventilation and adhere to safety measures. Pay attention to wind conditions and take precautions to prevent fire hazards in dry or flammable environments.