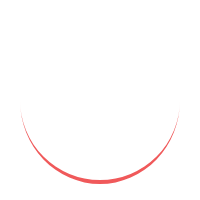
The process of selecting the right components for a project or assembly can be time-consuming and overwhelming, especially when dealing with a large inventory. However, with the advent of technology, a solution called a parts picker has emerged to simplify this process. In this article, we will explore what a parts picker is, how it works, its benefits, key features to consider, and tips for efficient utilization.
Introduction
In today's fast-paced world, efficiency is crucial in various industries. Whether it's manufacturing, electronics, or even DIY projects, the ability to select and procure the right components quickly can significantly impact productivity and success. This is where a parts picker comes into play.
What is a Parts Picker?
A parts picker is a software or tool designed to assist in the selection and retrieval of components from an inventory. It simplifies the process by providing a user-friendly interface that allows users to search, filter, and locate specific parts based on their requirements. The tool can be utilized in various industries, including manufacturing plants, warehouses, and retail stores.
How Does a Parts Picker Work?
A parts picker typically operates through a database that contains detailed information about each component in the inventory. This database is organized using various parameters such as part numbers, descriptions, specifications, and categories. Users can input their requirements into the parts picker, which then uses an algorithm to search the database and provide a list of matching components. The user can further refine the search using filters such as price, availability, or specific attributes.
Benefits of Using a Parts Picker
Using a parts picker offers several benefits, including:
1. Time-saving:
A parts picker significantly reduces the time required for component selection. Instead of manually searching through catalogs or databases, users can quickly find the right parts with a few clicks, allowing them to focus on other critical tasks.
2. Improved accuracy:
With a parts picker, the chances of human error during component selection are minimized. The tool ensures that users are presented with accurate and relevant options, reducing the risk of selecting incompatible or incorrect components.
3. Enhanced productivity:
By streamlining the component selection process, a parts picker improves overall productivity. Users can quickly assemble bill of materials (BOMs) or create orders, allowing for faster production cycles and reduced downtime.
4. Cost efficiency:
Efficient component selection leads to better cost control. A parts picker allows users to compare prices, choose alternatives, and optimize procurement decisions, resulting in potential cost savings.
Key Features to Look for in a Parts Picker
When considering a parts picker, it's essential to evaluate its features to ensure it meets your specific needs. Here are some key features to look for:
1. Intuitive user interface:
A user-friendly interface makes it easier for individuals with varying levels of technical expertise to navigate and utilize the parts picker effectively.
2. Advanced search capabilities:
A robust search function enables users to find components using keywords, part numbers, attributes, or even images. The ability to apply filters and narrow down search results is also beneficial.
3. Comprehensive database:
The parts picker should have an extensive database that includes a wide range of components from various manufacturers. The more comprehensive the database, the higher the chances of finding the required parts.
4. Integration with other systems:
Consider whether the parts picker can integrate with other systems such as enterprise resource planning (ERP) software or inventory management tools. Integration allows for seamless data transfer and synchronization, reducing duplication of efforts.
Factors to Consider When Choosing a Parts Picker
When selecting a parts picker, there are several factors to consider:
1. Scalability:
Ensure that the parts picker can accommodate your future needs as your inventory expands. It should be capable of handling a growing database and increased user traffic.
2. Customization options:
Look for a parts picker that can be customized to match your specific requirements. The ability to add custom fields, modify search parameters, or tailor the interface can significantly enhance usability.
3. Vendor support:
Consider the level of support provided by the parts picker vendor. Reliable technical assistance, regular updates, and responsiveness to user feedback are crucial for a smooth and efficient experience.
Common Challenges with Parts Pickers
While parts pickers offer numerous benefits, they can also come with some challenges:
1. Data accuracy:
Maintaining accurate and up-to-date data within the parts picker database can be a challenge, especially when dealing with a large number of components. Regular data audits and updates are necessary to ensure reliable search results.
2. Compatibility issues:
Components may have complex compatibility requirements, and ensuring accurate matching can be challenging. It's important to regularly update the parts picker's algorithm to account for new components and their compatibility rules.
Tips for Efficiently Using a Parts Picker
To maximize the efficiency of your parts picker usage, consider the following tips:
1. Familiarize yourself with the tool:
Invest time in learning and exploring all the features and functionalities of the parts picker. This will enable you to utilize its capabilities to their fullest potential.
2. Utilize search filters:
Leverage the search filters available in the parts picker to narrow down your results and quickly find the components you need. Filters such as price range, availability, or specific attributes can be incredibly useful.
3. Maintain data accuracy:
Regularly review and update the data within the parts picker's database to ensure accurate and reliable search results. Remove outdated components and add new ones as necessary.
Best Practices for Maintaining a Parts Picker
To ensure the longevity and efficiency of your parts picker, follow these best practices:
1. Regular backups:
Frequently back up the parts picker's database to prevent data loss in case of system failures or other unexpected events.
2. Periodic updates:
Stay updated with the latest software releases and updates provided by the parts picker vendor. These updates often include bug fixes, security patches, and new features.
Parts Picker FAQs
1. Is a parts picker suitable for small-scale projects or only for large inventories?
A parts picker can be beneficial for projects of any scale. Even for small-scale projects, the tool can save time and ensure accuracy in component selection.
2. Can a parts picker handle complex compatibility requirements?
Yes, a well-designed parts picker can handle complex compatibility requirements by incorporating detailed specifications and compatibility rules into its algorithm.
3. How often should I update the parts picker's database?
Regular updates are essential to maintain accurate data. It's recommended to conduct audits and updates on a periodic basis, depending on the frequency of changes in your inventory.
4. Can a parts picker integrate with my existing inventory management system?
Many parts pickers offer integration capabilities. It's important to check with the vendor to ensure compatibility with your specific inventory management system.
5. Is training required to use a parts picker effectively?
While some level of training may be beneficial, most parts pickers are designed to be user-friendly and intuitive. Exploring the tool's features and experimenting with its functionalities can help users become proficient quickly.