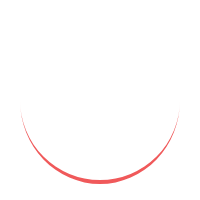
Oxy fuel gas cutters operate based on the principle of rapid oxidation. The torch combines oxygen and a fuel gas, such as acetylene or propane, in a controlled manner. As the oxygen interacts with the fuel gas, a chemical reaction occurs, generating an intense flame with temperatures reaching up to 6,000 degrees Fahrenheit (3,315 degrees Celsius). This heat melts the metal, and a high-pressure stream of oxygen blows away the molten material, resulting in a precise and clean cut.
Advantages of Oxy Fuel Gas Cutters
Oxy fuel gas cutters offer several advantages that make them a popular choice among professionals in various industries.
Versatility and Portability
One of the significant advantages of oxy fuel gas cutters is their versatility. These cutters can handle a wide range of materials, including carbon steel, stainless steel, aluminum, and even some non-ferrous metals. Moreover, they are highly portable, allowing operators to carry out cutting tasks in different locations easily.
Cost-Effectiveness
Oxy fuel gas cutters are known for their cost-effectiveness. The equipment itself is relatively affordable compared to some other cutting methods. Additionally, the fuel gases used, such as acetylene or propane, are readily available and reasonably priced, making oxy fuel gas cutting an economical choice for many applications.
Clean and Precise Cuts
When it comes to achieving clean and precise cuts, oxy fuel gas cutters excel. The intense heat of the flame, combined with the focused oxygen stream, ensures minimal slag formation and reduced dross, resulting in high-quality cuts with minimal post-cutting cleanup required.
Applications of Oxy Fuel Gas Cutters
The versatility and cutting precision of oxy fuel gas cutters make them indispensable in various industries and applications.
Metal Fabrication and Construction
In metal fabrication and construction, oxy fuel gas cutters find extensive use. Whether it's cutting steel beams, removing sections of metal during renovation projects, or creating intricate designs on metal sheets, oxy fuel gas cutters offer the flexibility and accuracy needed to meet the demands of these tasks.
Automotive and Shipbuilding Industries
Oxy fuel gas cutters are widely employed in the automotive and shipbuilding industries. From dismantling old vehicles and salvaging usable parts to cutting and shaping metal sheets for ship construction, oxy fuel gas cutters play a vital role in these sectors, offering efficiency and reliability.
Demolition and Salvage Operations
During demolition and salvage operations, oxy fuel gas cutters prove invaluable in cutting through thick metal structures, such as beams, pipes, and tanks. Their ability to handle heavy-duty cutting tasks and make precise cuts ensures the safe and efficient dismantling of structures.
Choosing the Right Oxy Fuel Gas Cutter
Selecting the appropriate oxy fuel gas cutter depends on several key factors.
Gas Selection: Acetylene or Propane
The choice between acetylene and propane as the fuel gas depends on the specific requirements of the cutting task. Acetylene provides a higher flame temperature, making it suitable for cutting thicker metals. Propane, on the other hand, offers better portability and is often favored for outdoor applications.
Cutting Capacity and Torch Design
Considering the cutting capacity and torch design is crucial to ensure the oxy fuel gas cutter can handle the desired thickness and type of metal. Different torch tips and nozzles are available to accommodate various cutting requirements.
Safety Features and Regulations
It is essential to choose an oxy fuel gas cutter that includes safety features such as flashback arrestors, check valves, and regulators. Additionally, adhering to safety regulations and guidelines is crucial to ensure the well-being of operators and the surrounding environment.
Proper Setup and Operation of Oxy Fuel Gas Cutters
To maximize the performance and safety of oxy fuel gas cutters, proper setup and operation are necessary.
Preparing the Workpiece and Workspace
Before initiating the cutting process, ensure that the workpiece is clean and free from contaminants. Adequate ventilation in the workspace is essential to prevent the accumulation of flammable gases and fumes.
Assembling and Adjusting the Equipment
Assemble the oxy fuel gas cutter components according to the manufacturer's instructions. Ensure all connections are secure and leak-free. Adjust the flame settings, gas pressures, and flow rates based on the recommended values for the specific material being cut.
Safety Measures and Personal Protective Equipment
Operators must follow proper safety measures and wear appropriate personal protective equipment (PPE). This includes flame-resistant clothing, goggles or face shields, gloves, and respiratory protection if required.
Tips for Efficient and Effective Oxy Fuel Gas Cutting
To achieve efficient and effective cutting results, consider the following tips:
Maintaining the Correct Flame Settings
Adjust the flame settings to maintain the correct balance between the fuel gas and oxygen. The flame should be sharp, focused, and not excessively oxidizing or carburizing.
Controlling the Cutting Speed
Maintain a steady cutting speed to ensure a clean and precise cut. Moving the torch too slowly can result in excessive heat transfer and potential warping, while moving it too quickly may lead to an incomplete cut.
Handling and Positioning the Torch Properly
Hold the torch steadily and maintain the appropriate angle while cutting. Maintaining proper distance between the torch and the workpiece helps to control the heat and prevent damage.
Common Challenges and Troubleshooting Tips
Oxy fuel gas cutting may sometimes face challenges that can impact the cutting process. Here are some common issues and troubleshooting tips:
Backfire and Flashback
Backfire and flashback can occur when the flame propagates back into the torch or hose. To prevent this, ensure the flashback arrestor is properly installed, maintain the correct gas pressures, and regularly inspect and clean the equipment.
Poor Cut Quality
Poor cut quality can result from factors such as incorrect flame settings, improper torch positioning, or worn-out consumables. Check and adjust the flame settings, maintain a steady hand position, and replace worn-out consumables as necessary.
Excessive Slag Formation
Excessive slag formation can occur when the cutting speed is too slow or the torch angle is incorrect. Adjust the cutting speed and maintain the proper torch angle to reduce slag formation and achieve cleaner cuts.
Maintenance and Care of Oxy Fuel Gas Cutters
Regular maintenance and care are vital for extending the lifespan and ensuring optimal performance of oxy fuel gas cutters.
Regular Inspection and Cleaning
Inspect the oxy fuel gas cutter regularly for any signs of damage, leaks, or wear. Clean the torch and replace consumable parts as needed. Lubricate moving components to ensure smooth operation.
Proper Storage and Handling of Equipment
Store oxy fuel gas cutters in a dry and secure location, away from flammable materials. Properly secure and protect hoses to prevent damage. Handle the equipment with care to avoid accidental drops or impacts.
Replacement of Consumables
Regularly replace consumable parts such as cutting tips, nozzles, and filters to maintain cutting quality and ensure safety. Follow the manufacturer's guidelines for the recommended replacement intervals.
Oxy Fuel Gas Cutter FAQs
Q1. Can oxy fuel gas cutters be used for cutting non-ferrous metals?
Yes, oxy fuel gas cutters can effectively cut non-ferrous metals such as aluminum, copper, and brass. However, it is important to select the appropriate fuel gas and adjust the cutting parameters accordingly to achieve optimal results.
Q2. Are there any environmental considerations when using oxy fuel gas cutters?
Oxy fuel gas cutting produces heat, light, and noise. While the process itself does not produce harmful emissions, it is essential to ensure proper ventilation in the workspace to dissipate any fumes or gases generated during the cutting process.
Q3. Can oxy fuel gas cutters be used for underwater cutting?
Yes, oxy fuel gas cutters can be used for underwater cutting applications. Special torch designs and equipment are available to ensure efficient cutting performance in underwater environments.
Q4. How long do the consumable parts of oxy fuel gas cutters typically last?
The lifespan of consumable parts, such as cutting tips and nozzles, can vary depending on factors such as cutting frequency, material thickness, and operator technique. It is advisable to follow the manufacturer's guidelines and replace consumables when they show signs of wear or degradation.
Q5. Can oxy fuel gas cutters be used for precision cutting applications?
While oxy fuel gas cutters offer precise cutting capabilities, they may not be suitable for applications that require extremely high levels of precision. For such applications, alternative cutting methods like plasma cutting or laser cutting may be more appropriate.