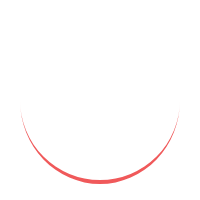
Plate bending machines are essential equipment used in various industries for bending metal plates. They are commonly used in fabrication shops, manufacturing plants, and construction sites. In this article, we will explore the role of an operator working with a plate bending machine, their responsibilities, required skills, safety considerations, and best practices for efficient operation.
What is a Plate Bending Machine?
A plate bending machine, also known as a plate roll or a sheet bending machine, is a mechanical device designed to bend metal plates into various shapes and curves. It is primarily used for applications where precision and accuracy are crucial, such as in the manufacturing of cylindrical tanks, pipes, and cones. Plate bending machines are capable of handling a wide range of materials, including steel, aluminum, and stainless steel.
Types of Plate Bending Machines
There are several types of plate bending machines available, each with its own unique features and advantages. The most common types include:
Three-Roll Plate Bending Machine
The three-roll plate bending machine consists of three rollers positioned in a triangular formation. Two bottom rollers are fixed, while the top roller can move vertically. The plate to be bent is placed between the rollers, and as the top roller exerts downward pressure, the plate is gradually bent into the desired shape. This type of machine is suitable for bending plates with a consistent thickness throughout.
Four-Roll Plate Bending Machine
The four-roll plate bending machine has an additional bottom roller compared to the three-roll machine. The four rollers are arranged in a pyramid formation, with the two lower rollers providing support and the upper rollers responsible for the bending action. This design offers increased precision and eliminates the need for pre-bending, making it ideal for bending thick plates and achieving complex shapes.
Double Pinch Plate Bending Machine
The double pinch plate bending machine, also known as a three-roll double-pinch machine, is similar to the three-roll machine but with a unique feature. In this machine, the top and bottom rollers are driven independently, allowing the operator to pre-bend the plate at both ends before the final bending process. This type of machine is commonly used for bending long plates or when precise control over the curvature is required.
Working Principle of Plate Bending Machine
The working principle of a plate bending machine involves the gradual bending of a metal plate between rollers. The operator adjusts the position of the rollers based on the desired curvature and feeds the plate into the machine. As the plate passes through the rollers, it undergoes plastic deformation, resulting in the desired bent shape. The operator controls the bending process, monitoring the alignment, speed, and pressure to achieve the desired outcome.
Responsibilities of an Operator
As an operator of a plate bending machine, you have several crucial responsibilities to ensure safe and efficient operation. These responsibilities include:
Machine Setup and Preparation
Before starting the bending process, the operator must set up the machine according to the specifications provided. This includes adjusting the roller positions, selecting the appropriate tooling, and ensuring the machine is in optimal working condition. Proper setup helps minimize errors and ensures accurate bending results.
Material Handling
The operator is responsible for handling the metal plates to be bent. This involves safely loading and unloading the plates onto the machine, ensuring proper alignment and positioning. Adequate care must be taken to prevent damage to the plates and ensure they are securely held during the bending process.
Machine Operation
During the bending process, the operator operates the machine, controlling the speed, pressure, and alignment to achieve the desired bending result. They monitor the machine's performance, making adjustments as necessary to maintain accuracy and quality.
Quality Control
The operator performs regular quality checks on the bent plates, ensuring they meet the required specifications and tolerances. They inspect for any defects, such as cracks, uneven bending, or surface imperfections, and make necessary adjustments to rectify any issues.
Maintenance and Troubleshooting
The operator is responsible for the maintenance and upkeep of the plate bending machine. This includes routine maintenance tasks, such as lubrication, cleaning, and inspection, to ensure the machine operates smoothly. In case of any malfunctions or breakdowns, the operator troubleshoots the issues or reports them to the maintenance department for repairs.
Essential Skills and Qualities
Being an operator of a plate bending machine requires a combination of technical skills and personal qualities. Some essential skills and qualities include:
Technical Knowledge: A solid understanding of the plate bending machine's operation, including its controls, settings, and tooling, is crucial. Operators should be familiar with different bending techniques and have the ability to interpret technical drawings and specifications.
Attention to Detail: Precision is essential in plate bending, and operators must have a keen eye for detail. They should be able to spot any deviations from the desired shape or specifications and make adjustments accordingly.
Problem-Solving Skills: Plate bending processes can present challenges, such as material inconsistencies or equipment malfunctions. Operators should possess good problem-solving skills to identify and resolve issues effectively.
Physical Fitness: Operating a plate bending machine often involves standing for extended periods, lifting heavy plates, and maneuvering equipment. Physical fitness and strength are important to perform the job safely and efficiently.
Safety Consciousness: Operators must prioritize safety at all times. They should be knowledgeable about safety procedures, including the use of personal protective equipment (PPE) and machine safety features, and be proactive in identifying and addressing potential hazards.
Safety Considerations
Safety is paramount when operating a plate bending machine. Operators must adhere to strict safety guidelines to prevent accidents and injuries. Some important safety considerations include:
Personal Protective Equipment (PPE)
Operators should wear appropriate PPE, including safety glasses, gloves, and protective footwear, to protect themselves from potential hazards such as flying debris, sharp edges, or accidental contact with moving parts.
Machine Safety Features
Plate bending machines are equipped with various safety features, such as emergency stop buttons, safety interlocks, and guards. Operators must familiarize themselves with these features and use them correctly to prevent accidents.
Best Practices for Efficient Operation
To ensure efficient operation and achieve optimal results, operators should follow these best practices:
Proper Machine Alignment
Before starting the bending process, the operator should ensure the machine is correctly aligned. Misalignment can lead to inaccurate bending and compromised quality. Regular checks and adjustments should be made to maintain proper alignment.
Correct Material Positioning
Precise positioning of the metal plate within the machine is crucial for accurate bending. Operators should carefully align the plate, making sure it is securely held by the rollers and positioned according to the bending requirements.
Optimal Machine Settings
Operators should have a thorough understanding of the machine's controls and settings. By selecting the appropriate bending parameters, such as roller pressure, speed, and curvature, they can achieve the desired bending results efficiently.
Regular Equipment Maintenance
To keep the plate bending machine in optimal condition, regular maintenance is essential. This includes lubricating moving parts, inspecting for wear and tear, and addressing any issues promptly. Well-maintained equipment operates more efficiently and has a longer lifespan.
Common Challenges and Troubleshooting Tips
Operating a plate bending machine can present various challenges. Here are some common challenges and tips for troubleshooting:
Uneven Bending: If the plate exhibits uneven bending, it could be due to misaligned rollers or inconsistent material thickness. Check the alignment and make necessary adjustments. Ensure the plate is of uniform thickness throughout.
Cracks or Wrinkles: Cracks or wrinkles on the bent plate can result from excessive pressure or improper material positioning. Reduce the pressure or adjust the plate's position to avoid these issues.
Material Slippage: If the material slips or moves during the bending process, it may lead to inaccuracies. Check that the rollers provide sufficient grip and adjust as needed. Proper material handling and alignment are crucial to prevent slippage.
Machine Jamming: In case of a machine jam, stop the operation immediately and identify the cause. Common causes include foreign objects, misaligned rollers, or mechanical issues. Clear the jam, realign if necessary, and ensure smooth operation before proceeding.
Operator Plate Bending Machine FAQs
1. How do I become a plate bending machine operator?
To become a plate bending machine operator, it is beneficial to have a background in mechanical or industrial engineering. Some technical schools and vocational training centers offer specific courses in machine operation. Hands-on experience and on-the-job training are also valuable in gaining proficiency in operating plate bending machines.
2. What is the average salary for a plate bending machine operator?
The average salary for a plate bending machine operator can vary depending on factors such as experience, location, and industry. However, in general, plate bending machine operators can earn a competitive salary that ranges from $30,000 to $50,000 per year.
3. Can a plate bending machine operator work in different industries?
Yes, plate bending machine operators can find employment opportunities in various industries that involve metal fabrication and manufacturing. Industries such as automotive, aerospace, construction, and shipbuilding often require the services of skilled plate bending machine operators.
4. Is plate bending machine operation physically demanding?
Operating a plate bending machine can be physically demanding as it involves standing for extended periods, lifting heavy plates, and maneuvering equipment. Physical fitness and strength are important for operators to perform their tasks safely and effectively.
5. Are plate bending machines safe to use?
Plate bending machines are designed with safety features and guidelines to ensure safe operation. However, it is crucial for operators to follow proper safety procedures, use personal protective equipment (PPE), and receive adequate training to minimize the risk of accidents and injuries.