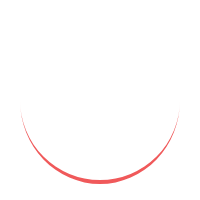
In the world of machining, conventional milling is a widely used technique that allows operators to produce precise and accurate parts. This article will delve into the intricacies of conventional milling, exploring its benefits, operation, safety considerations, troubleshooting, and more.
Introduction to Conventional Milling
Conventional milling is a subtractive manufacturing process that involves the removal of material from a workpiece using rotary cutters. Unlike other milling techniques, such as CNC milling, conventional milling requires the presence of a skilled operator to manually control the machine's movements and adjust the cutting parameters.
How Conventional Milling Works
In conventional milling, an operator plays a pivotal role in ensuring the milling process is carried out accurately. The operator sets up the milling machine, positions the workpiece, and selects appropriate cutting tools. During the operation, the operator controls the feed rate, depth of cut, and cutting speed to achieve the desired outcome.
Advantages of Conventional Milling
Conventional milling offers several advantages that make it a preferred choice for many machining tasks.
Versatility in Material and Tooling Choices
One significant advantage of conventional milling is its versatility. It can handle a wide range of materials, including metals, plastics, and composites. Additionally, operators have the flexibility to choose from various cutting tools, such as end mills, face mills, and slot drills, depending on the specific requirements of the project.
Cost-Effectiveness
Compared to CNC milling, conventional milling is often more cost-effective, particularly for small-scale or low-volume production. The initial investment for a conventional milling machine is generally lower, and the maintenance costs are usually less demanding.
Suitable for Various Workpiece Sizes
Conventional milling can accommodate workpieces of different sizes and shapes. Whether it's a large metal block or a small intricate part, operators can adapt the milling process accordingly to achieve the desired results.
Understanding the Milling Process
To excel in conventional milling, it's essential to grasp the fundamental principles of the milling process.
Cutting Tools and Their Types
Various cutting tools are utilized in conventional milling, each serving a specific purpose. End mills are commonly used for general milling operations, while face mills excel at producing flat surfaces. Slot drills are ideal for creating slots or pockets in the workpiece. By selecting the appropriate cutting tool, operators can optimize their milling process.
Feed Rates and Depth of Cut
The feed rate and depth of cut are critical parameters in conventional milling. The feed rate determines the speed at which the cutting tool advances through the workpiece, while the depth of cut controls the amount of material removed in a single pass. Finding the right balance between these parameters is crucial to achieving optimal results.
Chip Formation
During conventional milling, chips are formed as the cutting tool removes material from the workpiece. Understanding chip formation is vital for preventing chip clogging, maintaining surface quality, and prolonging tool life. Proper chip evacuation techniques, such as using appropriate coolant or air blasts, can enhance the overall milling process.
Tips for Successful Conventional Milling
To achieve successful milling results, operators should consider the following tips:
Choosing the Right Cutting Parameters
Selecting the appropriate cutting parameters, such as cutting speed, feed rate, and depth of cut, is crucial for efficient conventional milling. Operators should consult machining guidelines, tooling catalogs, or seek advice from tool manufacturers to optimize the cutting parameters based on the material and desired outcomes.
Proper Machine Maintenance
Regular maintenance of the milling machine is essential for consistent performance. Lubricating the moving parts, checking for wear and tear, and ensuring proper alignment of the machine components contribute to the longevity and accuracy of the milling process.
Effective Workpiece Clamping
Proper clamping of the workpiece ensures stability during milling operations. Using suitable clamping devices, such as vises or fixtures, prevents workpiece movement, reduces vibrations, and enhances overall machining precision.
Safety Considerations for Conventional Milling
Safety should always be a top priority when operating milling machines. Here are some important safety considerations:
Personal Protective Equipment (PPE)
Operators must wear appropriate personal protective equipment, including safety glasses, ear protection, and gloves, to safeguard themselves from potential hazards such as flying chips, noise, and tool mishaps.
Safe Operating Practices
Following safe operating practices is vital to minimize accidents. Operators should be familiar with the milling machine's controls, avoid wearing loose clothing or jewelry, and maintain a clean and organized workspace to prevent tripping hazards.
Risk Assessment and Hazard Mitigation
Conducting a thorough risk assessment before starting any milling operation is crucial. Identifying potential hazards and implementing appropriate mitigation measures, such as machine guarding, can significantly reduce the risk of accidents and injuries.
Conventional Milling vs. Other Milling Techniques
Understanding the differences between conventional milling and other milling techniques helps operators make informed decisions about the most suitable approach for their specific needs.
Conventional vs. CNC Milling
Compared to conventional milling, CNC milling offers automation and precision through computer-controlled movements. CNC machines follow pre-programmed instructions, making them ideal for high-volume production and complex geometries. However, conventional milling provides more hands-on control and is often preferred for smaller projects or prototyping.
Conventional vs. Climb Milling
In conventional milling, the cutting tool rotates against the direction of the workpiece feed. In contrast, climb milling involves the cutting tool rotating in the same direction as the feed. Climb milling offers benefits such as reduced cutting forces and improved surface finish, but it requires careful setup and machine rigidity.
Conventional vs. Face Milling
Face milling is a variation of conventional milling that focuses on producing flat surfaces. It involves using a face mill cutter, which has multiple inserts to remove material in a large area. Face milling is suitable for applications where surface finish and flatness are critical.
Common Challenges and Troubleshooting
Despite its advantages, conventional milling can present certain challenges. Here are some common issues and troubleshooting tips:
Surface Finish Issues
Poor surface finish can result from factors such as incorrect cutting parameters, tool wear, or improper tool selection. Operators should review their cutting parameters, ensure proper tool sharpness, and select suitable tool coatings or geometries to achieve the desired surface finish.
Chatter and Vibration
Chatter and vibration during milling can lead to poor surface quality, tool wear, and reduced tool life. To mitigate these issues, operators can adjust cutting parameters, increase machine rigidity, use anti-vibration tool holders, or consider implementing damping techniques.
Tool Wear and Breakage
Tool wear and breakage are common challenges in milling operations. Regular inspection of the cutting tools, proper selection of cutting parameters, and utilizing tool coatings or materials designed for specific applications can help minimize tool wear and prolong tool life.
Operator - Conventional Milling FAQs
What is the difference between conventional milling and climb milling?
In conventional milling, the cutting tool rotates against the direction of the workpiece feed, while in climb milling, the tool rotates in the same direction as the feed. Climb milling offers advantages like reduced cutting forces and improved surface finish.
Can I use conventional milling for hard materials like stainless steel?
Yes, conventional milling can be used for machining hard materials like stainless steel. However, operators should ensure appropriate cutting parameters, use suitable cutting tools, and consider factors like tool wear and heat generation.
How often should I lubricate the milling machine?
Lubrication frequency depends on the machine manufacturer's recommendations and the intensity of usage. Generally, regular lubrication at designated intervals, along with visual inspections, helps maintain machine performance and longevity.
What safety precautions should I take while operating a milling machine?
Safety precautions include wearing personal protective equipment (PPE), being familiar with machine controls, maintaining a clean workspace, and conducting risk assessments. Following safe operating practices and implementing machine guarding measures are also essential.
What are some common signs of tool wear in conventional milling?
Signs of tool wear include poor surface finish, increased cutting forces, excessive noise or vibration, and reduced dimensional accuracy. Regular inspection and monitoring of the tool's cutting edges are crucial to identify and address tool wear issues promptly.