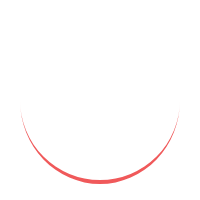
CNC Electric Discharge Machines (EDMs) are widely used in the manufacturing industry for precision machining applications. These machines utilize electrical sparks to erode the material and create complex shapes and cavities with high accuracy. In this article, we will explore the functionality, advantages, applications, and maintenance considerations of CNC EDMs.
A CNC Electric Discharge Machine (EDM) is a computer-controlled machining tool that utilizes electrical discharges to shape and machine conductive materials. It employs a series of controlled sparks between an electrode and the workpiece to remove material through the process of spark erosion. The CNC aspect allows for precise control over the machine's movements, enabling complex shapes and cavities to be produced with exceptional accuracy.
How does a CNC EDM work?
CNC EDMs rely on the principle of spark erosion, where electrical discharges occur between the electrode and the workpiece. The machine uses a power supply to generate a series of high-frequency electrical pulses. These pulses create a potential difference between the electrode and the workpiece, resulting in the formation of an electrical spark.
The spark heats the surrounding environment to an extremely high temperature, causing the material to melt and evaporate. The molten material is then flushed away by a dielectric fluid, typically deionized water, which acts as a coolant and removes debris from the machining area. By precisely controlling the spark's duration and intensity, the CNC EDM can selectively remove material and shape the workpiece.
Advantages of CNC EDMs
CNC EDMs offer several advantages that make them suitable for various applications in the manufacturing industry:
High Precision: CNC EDMs can achieve exceptional levels of precision, often in the range of micrometers. This makes them ideal for manufacturing intricate components with tight tolerances.
Complex Geometries: The spark erosion process allows CNC EDMs to create complex shapes and cavities that are difficult to achieve with traditional machining methods.
No Contact Cutting: Unlike conventional cutting tools, CNC EDMs do not make physical contact with the workpiece. This eliminates the risk of tool wear and allows for machining delicate or fragile materials.
Hard Material Machining: CNC EDMs can effectively machine hard materials such as hardened steel, titanium, and carbide. This makes them invaluable in industries where hardness and durability are critical.
Minimal Material Stress: Since CNC EDMs do not generate cutting forces, they minimize material stress and reduce the risk of distortion or deformation.
Applications of CNC EDMs
CNC EDMs find applications in various industries where precision machining is required. Some common applications include:
Mold Making: CNC EDMs are extensively used in the production of molds for plastic injection molding, die casting, and forging processes. They can create intricate mold cavities with high precision.
Aerospace: CNC EDMs play a crucial role in manufacturing aerospace components such as turbine blades, fuel nozzles, and complex engine parts.
Medical Industry: CNC EDMs are utilized in the production of surgical instruments, orthopedic implants, and dental prosthetics, where high precision is paramount.
Tool and Die Making: CNC EDMs are essential in the fabrication of cutting tools, punches, dies, and other tooling components that require intricate shapes and precise tolerances.
Electronics: CNC EDMs are used for producing intricate electrical contacts, connectors, and microelectromechanical systems (MEMS).
Types of CNC EDMs
There are several types of CNC EDMs, each suited for specific machining applications. The most common types include:
Wire EDM
Wire EDM, also known as Wire Cut EDM, uses a thin, electrically conductive wire as the electrode. The wire is continuously fed through the workpiece, creating a cut or contour defined by the CNC program. Wire EDM is particularly effective for producing complex shapes and thin features.
Sinker EDM
Sinker EDM, also called Ram EDM or Conventional EDM, uses a specially shaped electrode to erode the workpiece. The electrode is immersed in a dielectric fluid, and controlled sparks occur between the electrode and the workpiece. Sinker EDM is ideal for machining deep cavities and complex molds.
Hole Drilling EDM
Hole Drilling EDM, also known as EDM Drilling or EDM Hole Popping, is used to create small, precise holes in conductive materials. This process is commonly employed in industries such as aerospace and automotive, where cooling and fuel systems require intricate hole patterns.
Choosing the right CNC EDM for your needs
When selecting a CNC EDM for your specific requirements, consider the following factors:
Machining Requirements: Determine the complexity of the parts you need to produce and the level of precision required. This will help you choose between wire EDM, sinker EDM, or hole drilling EDM.
Material Compatibility: Ensure that the CNC EDM is capable of machining the materials you work with. Different EDMs have varying capabilities when it comes to material hardness and conductivity.
Workpiece Size and Weight: Consider the size and weight of the components you intend to machine. Ensure that the CNC EDM can accommodate your workpiece dimensions.
Automation and Integration: Evaluate whether the CNC EDM can be integrated into your existing production workflow and if automation features are necessary for your operations.
Maintenance and Support: Look for a CNC EDM manufacturer or supplier that provides reliable technical support and maintenance services to minimize downtime.
Setting up and operating a CNC EDM
Proper setup and operation of a CNC EDM are crucial for achieving optimal results. Here are some key steps to follow:
Workpiece Preparation: Clean and secure the workpiece to the machine's worktable or fixture. Ensure that it is properly aligned and positioned.
Electrode Selection: Choose the appropriate electrode material and shape based on your machining requirements. The electrode should be securely mounted and aligned with the CNC EDM.
Dielectric Fluid: Fill the CNC EDM's reservoir with the recommended dielectric fluid, typically deionized water. Maintain the fluid's cleanliness and replace it regularly to ensure optimal performance.
CNC Programming: Create or import the CNC program that defines the machining operations, tool paths, and cutting parameters. Ensure that the program is error-free and properly validated.
Safety Precautions: Follow all safety protocols and guidelines provided by the CNC EDM manufacturer. Wear appropriate personal protective equipment (PPE) and ensure the machine is properly grounded.
Machine Calibration: Perform necessary calibration procedures to ensure the machine is accurately positioned and aligned. This includes homing, tool length measurement, and calibration of axes.
Run the Job: Start the machining process by initiating the CNC program. Monitor the process closely, periodically inspecting the workpiece and electrode wear. Make any necessary adjustments to optimize the machining.
Post-Machining Finishing: After the machining is complete, remove the workpiece and clean it thoroughly. Perform any required post-machining finishing operations, such as deburring or polishing.
Maintenance and safety considerations
To ensure the longevity and safety of your CNC EDM, regular maintenance is essential. Here are some maintenance tasks to consider:
Dielectric Fluid Maintenance: Regularly check the dielectric fluid level and quality. Replace the fluid when necessary and keep the reservoir clean.
Electrode Inspection and Replacement: Periodically inspect the electrode for wear or damage. Replace it when it no longer meets the required machining standards.
Machine Cleaning: Clean the machine, including the worktable, electrodes, and guides, to remove debris and prevent contamination.
Filter Replacement: If your CNC EDM has a filtration system, regularly replace the filters to maintain optimal performance and prevent clogging.
Scheduled Servicing: Adhere to the manufacturer's recommended servicing schedule, which may include lubrication, calibration, and other maintenance tasks.
In terms of safety considerations, follow these guidelines:
Always wear appropriate PPE, including safety glasses, gloves, and protective clothing.
Ensure the CNC EDM is properly grounded to prevent electrical hazards.
Familiarize yourself with emergency stop procedures and location.
Train operators on safe operating practices and the correct use of the machine.
Future trends in CNC EDM technology
The field of CNC EDM technology is constantly evolving, and several trends are shaping its future. Some noteworthy developments include:
Advancements in Automation: Automation capabilities in CNC EDMs are expanding, allowing for more efficient and unattended machining. This includes robotic integration, tool changers, and advanced workpiece handling systems.
Improved Machining Speed: Ongoing research and development efforts aim to increase the machining speed of CNC EDMs, reducing cycle times and enhancing productivity.
Enhanced Control and Monitoring: Future CNC EDMs are likely to offer improved control and monitoring features, allowing for real-time feedback, predictive maintenance, and process optimization.
Additive Manufacturing Integration: The integration of CNC EDMs with additive manufacturing techniques, such as 3D printing and laser deposition, is being explored. This combination can enable the creation of complex hybrid parts with high precision.
Operator - CNC Electric Discharge Machine Spark Erosion FAQs
Q: What materials can be machined with a CNC EDM?
A: CNC EDMs can machine a wide range of conductive materials, including hardened steel, stainless steel, aluminum, titanium, copper, and brass.
Q: How precise are CNC EDMs?
A: CNC EDMs are capable of achieving high precision, typically in the range of micrometers. The actual precision depends on factors such as the machine's design, control system, and cutting parameters.
Q: Is CNC EDM suitable for high-volume production?
A: CNC EDMs are generally more suitable for low- to medium-volume production due to the time required for spark erosion. However, advancements in automation and faster machining speeds are making them more viable for certain high-volume applications.
Q: Can CNC EDMs be automated?
A: Yes, CNC EDMs can be automated by integrating them with robotic systems, tool changers, and workpiece handling systems. Automation enhances productivity, allows for unattended machining, and reduces manual intervention.
Q: What are the common maintenance tasks for CNC EDMs?
A: Common maintenance tasks for CNC EDMs include dielectric fluid maintenance, electrode inspection and replacement, machine cleaning, filter replacement (if applicable), and adhering to the manufacturer's recommended servicing schedule. Regular maintenance ensures optimal performance and prolongs the machine's lifespan.