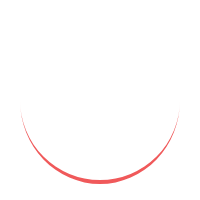
In the world of construction and infrastructure development, precision and efficiency are paramount. Traditional excavation methods can be time-consuming, costly, and disruptive to the surrounding environment. However, with the advent of operator-boring machines, the game has changed. These powerful machines have become an indispensable tool for various industries, offering unparalleled accuracy and efficiency in underground drilling and installation processes. In this article, we will explore the world of operator-boring machines, their applications, advantages, and how they are shaping the future of construction.
2. What is an Operator-Boring Machine?
An operator-boring machine is a specialized construction tool designed to create horizontal, vertical, or angled holes beneath the surface. Unlike traditional excavation methods, which involve digging trenches, operator-boring machines utilize a drilling head or cutting tool that can be guided and controlled to create tunnels in a predetermined path. These machines can bore holes of varying diameters and lengths, depending on the specific requirements of the project.
3. The Importance of Operator-Boring Machines in Construction
One of the primary reasons operator-boring machines have gained immense popularity in the construction industry is their ability to provide exceptional precision and accuracy. These machines can create tunnels with minimal deviation from the intended path, ensuring that utility lines and pipelines are installed exactly where required. This precision eliminates the risk of accidental damage to existing infrastructure and minimizes costly repairs and disruptions.
Increased Efficiency
Operator-boring machines significantly enhance project efficiency by reducing the time and labor required for underground installations. Traditional excavation methods often involve extensive manual labor and lengthy project timelines. In contrast, operator-boring machines streamline the process, allowing for faster completion of projects. By automating the drilling process, these machines eliminate the need for multiple workers and increase overall productivity.
Cost Savings
By expediting project timelines and reducing labor requirements, operator-boring machines can lead to substantial cost savings for construction companies. The decreased reliance on manual labor helps minimize wage expenses, while the accelerated completion of projects reduces overhead costs. Additionally, the precision of operator-boring machines minimizes the risk of expensive rework and repairs, further contributing to cost savings.
4. Types of Operator-Boring Machines
There are two primary types of operator-boring machines:
Horizontal boring machines are designed to create tunnels parallel to the ground surface. They are commonly used for laying underground utility lines, such as telecommunications cables, electrical conduits, and water pipes. These machines are highly versatile and can operate in a variety of soil conditions, making them a preferred choice for many construction projects.
Operator-Boring Machine
Vertical boring machines, as the name suggests, are used to create vertical tunnels or shafts. They are typically employed in mining operations, geotechnical investigations, and construction projects that require the installation of vertical infrastructure elements. Vertical boring machines are engineered to handle the challenges posed by deep drilling, ensuring safe and efficient excavation.
5. Applications of Operator-Boring Machines
The versatility of operator-boring machines allows for their application in various industries and projects. Some common applications include:
Construction Industry
In the construction industry, operator-boring machines play a vital role in the installation of underground utilities. They are used for laying water, gas, and sewer lines, as well as for creating tunnels for electrical and telecommunications infrastructure. The precise drilling capabilities of these machines enable the seamless integration of underground services with minimal disruption to existing structures.
Infrastructure Projects
Large-scale infrastructure projects, such as highways, railways, and airports, often require extensive underground work. Operator-boring machines are invaluable in such projects, enabling the installation of critical infrastructure without disrupting surface traffic or causing inconvenience to the public. These machines can create tunnels for drainage systems, fiber optic cables, and other necessary utilities.
Pipeline Installation
Operator-boring machines are extensively used in pipeline installation projects. Whether for oil and gas pipelines or water distribution networks, these machines offer a cost-effective and efficient alternative to traditional open-cut methods. By drilling precise tunnels beneath existing infrastructure and natural obstacles, pipelines can be laid without disturbing the surrounding environment.
Mining and Exploration
In the mining industry, operator-boring machines facilitate the extraction of valuable resources by creating shafts and tunnels for access and exploration. These machines enable safe and controlled excavation in deep underground mines, increasing operational efficiency and worker safety.
6. Advantages of Using Operator-Boring Machines
Compared to traditional excavation methods, operator-boring machines minimize surface disruption during the installation process. The ability to create underground tunnels without the need for extensive open trenches preserves the integrity of the surrounding environment, reducing the visual impact and disturbances to flora, fauna, and public spaces.
Environmentally Friendly
Operator-boring machines offer significant environmental benefits. By minimizing surface disturbance and the associated soil erosion, these machines help protect natural habitats and ecosystems. Additionally, the reduced reliance on heavy machinery and vehicle traffic contributes to lower carbon emissions, promoting sustainable construction practices.
Versatility
Operator-boring machines are highly versatile and can be utilized in various soil conditions and terrains. Whether it's soft soil, rocky terrain, or urban environments, these machines can adapt to different circumstances, ensuring successful drilling operations in diverse settings. The ability to customize drilling parameters and control the drilling path allows for efficient completion of projects, regardless of the site conditions.
7. Factors to Consider When Choosing an Operator-Boring Machine
When selecting an operator-boring machine for a project, several factors should be taken into consideration:
Project Requirements
Evaluate the specific requirements of the project, such as the required tunnel diameter, length, and depth. Choose a machine that aligns with these specifications to ensure optimal performance and accuracy.
Machine Size and Power
Consider the size and power of the machine. Larger machines are suitable for heavy-duty applications and deep drilling, while smaller machines offer greater maneuverability in tight spaces.
Durability and Reliability
Select a machine from a reputable manufacturer known for producing durable and reliable equipment. Operator-boring machines are long-term investments, and choosing a well-built machine will minimize downtime and maintenance costs.
Safety Features
Ensure that the machine incorporates essential safety features, such as emergency shutdown mechanisms, automatic overload protection, and operator safety controls. Safety should be a top priority in any construction operation.
8. Maintenance and Care for Operator-Boring Machines
Proper maintenance and care are crucial for maximizing the lifespan and performance of operator-boring machines. Consider the following maintenance practices:
Regular Inspections and Lubrication
Perform routine inspections of the machine to identify any signs of wear or damage. Lubricate moving parts as recommended by the manufacturer to prevent friction and ensure smooth operation.
Cleaning and Storage
Clean the machine after each use to remove debris and prevent corrosion. Store the machine in a dry and secure location to protect it from the elements and unauthorized access.
Professional Servicing
Engage qualified technicians for regular servicing and repairs. They can identify potential issues and perform necessary maintenance tasks to keep the machine in optimal condition.
9. Future Trends in Operator-Boring Machines
The field of operator-boring machines is constantly evolving, and several trends are shaping their future:
Advancements in Automation and Robotics
Automation and robotics are transforming the construction industry, and operator-boring machines are no exception. The integration of advanced automation technologies allows for greater precision, efficiency, and remote operation, reducing the need for direct human intervention.
Integration of GPS and Telematics
The incorporation of GPS and telematics technology enables real-time tracking and monitoring of operator-boring machines. This integration enhances project management by providing accurate data on machine location, drilling progress, and maintenance requirements.
11.Operator-Boring Machine Frequently Asked Questions
Q1: How deep can operator-boring machines drill?
Q2: Are operator-boring machines suitable for rocky terrains?
Q3: Can operator-boring machines be used for underwater drilling?
Q4: What safety precautions should operators take when using these machines?
Q5: Are operator-boring machines cost-effective compared to traditional excavation methods?