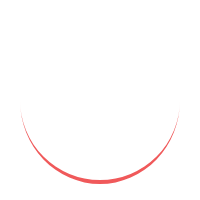
Grinders play a crucial role in the construction industry, providing workers with a versatile and efficient tool for various tasks. From cutting and shaping metal to preparing concrete surfaces, grinders are indispensable in construction projects. In this article, we will explore the different types of grinders, their applications in construction, safety considerations, maintenance tips, and the benefits they offer.
Grinders, also known as angle grinders or disc grinders, are handheld power tools that utilize abrasive discs or wheels to perform cutting, grinding, and polishing tasks. They are widely used in construction for their ability to handle tough materials and provide precise results. Grinders are powered by electricity, batteries, or compressed air, and their compact size and maneuverability make them ideal for construction sites.
A grinder is a mechanical tool that employs rotating discs or wheels with abrasive surfaces to remove material or create a desired shape or finish. It consists of a motor, a handle, and a rotating head where various types of discs can be attached.
Grinders are an essential tool in construction projects due to their versatility and efficiency. They enable workers to perform a wide range of tasks, including cutting, grinding, polishing, and surface preparation. Whether it's metal fabrication or concrete work, grinders are invaluable for achieving desired outcomes with precision and speed.
There are two primary types of grinders commonly used in construction: angle grinders and bench grinders. Each type has its own set of features and applications.
Angle grinders, also known as side grinders or disc grinders, are handheld tools with a rotating abrasive disc. They are versatile and widely used in construction for various tasks, such as cutting, grinding, and polishing.
Angle grinders are characterized by their compact size, lightweight design, and high-speed rotation. They typically have a range of disc sizes available, allowing for versatility in different applications. Angle grinders can be used for cutting through metal pipes, shaping steel rebars, removing weld slag, and even cutting tiles or bricks for precision fitting.
When using angle grinders, it is essential to follow safety precautions to prevent accidents and injuries. Always wear appropriate personal protective equipment (PPE), such as safety goggles, gloves, and a dust mask. Ensure that the work area is clear of obstructions, and secure the workpiece properly. It is crucial to maintain a firm grip on the grinder and avoid exerting excessive pressure, as it can cause kickbacks or loss of control.
Bench grinders are larger, stationary tools typically mounted on a workbench or pedestal. They consist of two grinding wheels, one coarse and one fine, that rotate in opposite directions.
Bench grinders are primarily used for sharpening, shaping, and smoothing metal objects. They are commonly employed in metal fabrication shops, allowing workers to maintain the sharpness of tools, remove burrs, or shape metal parts. Bench grinders are also useful for honing and grinding various cutting tools used in construction.
When using bench grinders, it is crucial to ensure proper safety measures. Always wear safety goggles and protective gloves. Make sure the grinding wheels are securely mounted and free from cracks or damage. Avoid applying excessive pressure or forcing the workpiece against the wheel, as it can cause overheating and wheel breakage.
Grinders find extensive applications in the construction industry, catering to tasks that involve metal fabrication and concrete preparation. Let's explore some common applications in more detail.
Metal Fabrication
In metal fabrication, grinders are essential tools for cutting, shaping, and finishing metal components. They offer the versatility required to work with various types of metal, including steel, aluminum, and stainless steel.
Cutting and Shaping Metal
Angle grinders equipped with cutting discs are widely used for precise metal cutting tasks. They can easily slice through metal sheets, pipes, or rebars, allowing workers to create custom shapes or fit pieces together accurately.
Removing Rust and Paint
Grinders with wire brush attachments or abrasive discs are excellent for removing rust, paint, and other surface coatings from metal. By removing these contaminants, the grinder prepares the metal surface for welding, painting, or further fabrication processes.
Grinders are instrumental in concrete preparation, enabling workers to achieve smooth and even surfaces for construction projects.
Surface Smoothing and Leveling
Angle grinders with diamond cup wheels or abrasive grinding discs are commonly used to smooth uneven concrete surfaces or level high spots. They can remove imperfections, such as bumps or ridges, providing a flat and polished finish.
Removing Coatings and Adhesives
In renovation projects, grinders are invaluable for removing old coatings, adhesives, or epoxy from concrete surfaces. The abrasive discs effectively strip away these layers, preparing the concrete for new applications such as painting or flooring installation.
When selecting a grinder for construction projects, several factors need to be considered to ensure optimal performance and safety.
Power Source
Grinders are available in different power options, including electric, battery-powered, and pneumatic (air-powered). Electric grinders are the most common, offering consistent power and reliable performance. Battery-powered grinders provide greater mobility but may have limited runtime. Pneumatic grinders are suitable for heavy-duty applications but require an air compressor.
Disc Size and Speed
The choice of disc size and speed depends on the specific task at hand. Smaller discs offer more precision, while larger discs are better for heavy material removal. Higher rotation speeds result in faster material removal but may require more experience to handle safely.
Additional Features and Accessories
Grinders may come with additional features, such as adjustable handles for improved ergonomics, dust collection systems for cleaner working environments, or variable speed settings for enhanced control. It is essential to assess these features based on the specific requirements of the construction project.
Safety is paramount when using grinders in construction. Adhering to proper safety precautions ensures the well-being of workers and prevents accidents.
Personal Protective Equipment (PPE)
Wearing appropriate PPE is crucial when operating grinders. This includes safety goggles or a face shield to protect the eyes from debris, protective gloves to safeguard hands, and a dust mask to prevent inhalation of fine particles.
Proper Handling and Operation
Workers should receive training on proper grinder handling and operation. This includes maintaining a secure grip, using the grinder at the appropriate angle, and avoiding excessive force. It is important to maintain control over the tool and avoid distractions while operating it.
Maintenance and Inspection
Regular maintenance and inspection of grinders are vital for their safe operation. Inspect the tool before each use, checking for any damage or loose parts. Ensure that the grinding discs are properly secured and in good condition. Lubricate moving parts as recommended by the manufacturer and keep the tool clean from dust and debris buildup.
Grinder Maintenance and Care
To prolong the lifespan and optimize performance, grinders require regular maintenance and care.
Cleaning and Lubrication
After each use, clean the grinder by removing dust and debris from the tool's exterior and ventilation areas. Avoid using compressed air for cleaning, as it can force debris into the internal components. Lubricate the grinder's moving parts as recommended by the manufacturer to ensure smooth operation.
Disc Replacement and Alignment
Inspect the grinding discs regularly for wear or damage. Replace worn-out discs promptly to maintain optimal cutting or grinding performance. When replacing the discs, ensure proper alignment and secure attachment to prevent accidents or disc dislodgment during operation.
The use of grinders in construction projects offers several benefits that contribute to improved efficiency and productivity.
Time and Labor Efficiency
Grinders enable faster material removal and surface preparation compared to manual methods. They allow construction workers to accomplish tasks more quickly, saving time and reducing labor costs. The precise and consistent results obtained with grinders also minimize the need for rework or corrections.
Versatility and Adaptability
Grinders are versatile tools that can be used for various applications in construction. With different types of discs or wheels, they can handle a wide range of materials and surface conditions. This adaptability makes grinders valuable assets in construction projects with diverse requirements.
1. What are the main safety precautions to follow when using a grinder in construction?
When using a grinder in construction, it is important to wear appropriate personal protective equipment (PPE), such as safety goggles, gloves, and a dust mask. Secure the workpiece properly and maintain a firm grip on the grinder. Avoid applying excessive pressure and follow proper handling and operation techniques.
2. Can grinders be used for tasks other than metal and concrete preparation?
Yes, grinders have applications beyond metal and concrete preparation. They can be used for tasks like cutting tiles, shaping wood, sharpening tools, and removing rust or paint from various surfaces.
3. How often should grinder discs be replaced?
Grinder discs should be replaced when they become worn, damaged, or when their cutting or grinding performance diminishes. Regularly inspect the discs and replace them as needed to ensure optimal results and safety.
4. Are there any specific maintenance practices for battery-powered grinders?
For battery-powered grinders, it is important to follow the manufacturer's recommendations for battery maintenance and charging. Keep the battery clean and properly stored when not in use. Regularly inspect the grinder's overall condition, including the battery connections, and address any issues promptly.
5. Can angle grinders be used for precision cutting and shaping?
Angle grinders can be used for precision cutting and shaping, especially when equipped with appropriate cutting discs or attachments. However, it requires experience and skill to achieve precise results, and it is recommended to use specialized tools for high-precision tasks whenever possible.