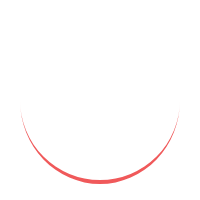
If you're in the business of manufacturing or selling gemstones, you know that the final shaping and calibrating process is crucial for producing a high-quality product that will attract customers. In this article, we'll explore the ins and outs of gemstone processing, with a focus on the final shaping and calibrating stage. We'll cover everything from the tools and techniques used to the benefits of using a final shaper and calibrator. So, let's dive in!
Introduction to Gemstone Processing
Before we get into the specifics of final shaping and calibrating, it's important to understand the basics of gemstone processing. This process involves several stages, including sawing, grinding, and polishing. The goal is to take a rough, uncut gemstone and transform it into a finished product that's ready for use in jewelry or other decorative items.
Gemstone Processing - Final Shaper and Calibrator The Importance of Final Shaping and Calibrating
While every stage of gemstone processing is important, final shaping and calibrating play a particularly crucial role. This stage involves using specialized tools and techniques to give the gemstone its final shape and size. This ensures that each gemstone in a batch is uniform in appearance and size, which is essential for creating high-quality products.
Gemstone Processing - Final Shaper and Calibrator Tools Used in Final Shaping and Calibrating
There are several tools used in the final shaping and calibrating process, each designed to achieve a specific goal. One of the most important tools is the faceting machine, which uses a series of diamond-coated wheels to shape and polish the gemstone. Other tools include a caliper, which is used to measure the gemstone's size and shape, and a dop stick, which holds the gemstone in place during the shaping process.
Gemstone Processing - Final Shaper and Calibrator Techniques Used in Final Shaping and Calibrating
In addition to specialized tools, there are also several techniques used in final shaping and calibrating. One of the most important is blocking, which involves using a saw to create a rough shape for the gemstone. Once the gemstone is blocked, it's placed on the faceting machine, where it undergoes a series of steps to create the final shape and size.
Gemstone Processing - Final Shaper and Calibrator Benefits of Using a Final Shaper and Calibrator
There are several benefits to using a final shaper and calibrator in the gemstone processing process. Perhaps the most important is the ability to create a uniform product that meets exact specifications. This not only ensures a high-quality finished product but also makes it easier to sell gemstones in bulk to manufacturers or other businesses.
Gemstone Processing - Final Shaper and Calibrator Common Challenges in Final Shaping and Calibrating
While final shaping and calibrating are essential for producing high-quality gemstones, there are also several challenges that can arise. One common issue is uneven cutting, which can result in a gemstone that's not uniform in size or shape. Other challenges include chipping or cracking of the gemstone during the shaping process.
Gemstone Processing - Final Shaper and Calibrator Best Practices for Final Shaping and Calibrating
To overcome these challenges, it's important to follow best practices during the final shaping and calibrating process. This includes using the right tools and techniques for each gemstone and ensuring that each one is carefully monitored throughout the process. It's also important to work with a skilled technician who has experience in gemstone processing and can identify potential issues before they become a problem.
Gemstone Processing - Final Shaper and Calibrator FAQs
What is gemstone processing?
Gemstone processing involves several stages, including sawing, grinding, and polishing, to transform a rough, uncut gemstone into a finished product.
What is the purpose of final shaping and calibrating?
Final shaping and calibrating ensure that each gemstone in a batch is uniform in appearance and size, which is essential for creating high-quality products.
What tools are used in final shaping and calibrating?
Tools used in this stage include a faceting machine, caliper, dop stick, and diamond-coated wheels.
What are some common challenges in final shaping and calibrating?
Uneven cutting, chipping, and cracking are common challenges that can arise during this process.
How can I ensure a successful final shaping and calibrating process?
Following best practices, such as using the right tools and techniques and working with a skilled technician, can help ensure a successful outcome.
About Us
The individual works with high-speed rotating Scaife machines with diamond or steel laps in order to give the pre-shaped gemstone the final shape as per planned weight and size. Final-shaping determines the shape, size, and weight of the final stone. The final shaper gives the final shape to a gemstone so that it is ready for faceting and/or polishing as per the customer’s requirement of exact shape, size, and weight. Shaping, sizing, and calibrating the pre-shaped gemstone is an essential part of the final shaper’s role.
JOB DESCRIPTION
The tasks a Gemstone Final Shaper & Calibrator is expected to perform include:
Giving the final shape to a gemstone so that it is ready for faceting and/or polishing
WORK ENVIRONMENT
It is a bench job
Need not handle a team
Travelling is not required
Part-time work and contractual work is available
Work from home option is not available
Working hours
Most companies usually work for 6 days a week and 8 hours every day. This may vary from company to company.
Shift system may be available in some organizations.
Most gemstone drillers are freelancers.