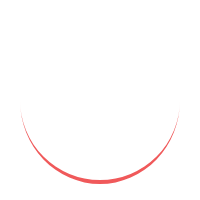
In today's competitive manufacturing landscape, companies strive to create products that are not only innovative and functional but also efficient to manufacture. This is where the role of a Design-For-Manufacture (DFM) engineer becomes vital. Design-For-Manufacture engineering is a discipline that focuses on optimizing product designs for efficient and cost-effective production processes. In this article, we will explore the responsibilities, skills, benefits, and challenges associated with being a Design-For-Manufacture engineer, along with the future trends in this field.
Design-For-Manufacture engineering, often abbreviated as DFM, is the practice of designing products with the manufacturing process in mind from the early stages of development. It involves collaborating closely with design and manufacturing teams to ensure that products can be produced efficiently without compromising quality or functionality. By considering manufacturing constraints during the design phase, DFM engineers can streamline production, reduce costs, and enhance the overall manufacturability of a product.
The primary role of a Design-For-Manufacture engineer is to bridge the gap between product design and manufacturing. They act as a liaison between the two teams, ensuring that the design intent is translated into a product that can be efficiently manufactured. DFM engineers work closely with designers, engineers, and manufacturing specialists to identify potential manufacturing challenges and find solutions that optimize the production process.
analyze product designs for manufacturability. They carefully review the design specifications, considering factors such as material selection, assembly methods, and production equipment requirements. By assessing the design's compatibility with manufacturing processes, they can identify potential issues or inefficiencies early on and propose modifications to enhance manufacturability.
DFM engineers also play a crucial role in optimizing designs for cost, quality, and efficiency. They evaluate different design alternatives, considering factors such as material costs, production time, and ease of assembly. By making informed decisions and collaborating with the design team, they can achieve the delicate balance between product functionality and manufacturability, ensuring that the final design is both cost-effective and meets the desired quality standards.
In addition to design analysis and optimization, DFM engineers conduct feasibility studies and risk assessments. They evaluate the technical feasibility of a design in terms of manufacturing processes and capabilities. This includes assessing the availability of materials, the capacity of production facilities, and any potential risks or bottlenecks that may arise during manufacturing. By identifying and addressing these issues early in the design phase, DFM engineers contribute to a smoother production process and mitigate potential delays or cost overruns.
To facilitate the manufacturing process, DFM engineers create detailed manufacturing guidelines. These guidelines provide instructions and specifications for production teams to follow, ensuring consistency and efficiency in manufacturing operations. They outline specific steps, assembly procedures, and quality control measures to ensure that the product is manufactured to the desired standards. By providing clear and comprehensive instructions, DFM engineers enable smooth transitions from design to production, minimizing errors and maximizing productivity.
Design-For-Manufacture engineering offers numerous benefits to companies across industries. By integrating DFM principles into the product development process, businesses can experience:
Reduced production costs and waste: By optimizing designs for manufacturing efficiency, DFM engineers identify opportunities to reduce material waste, minimize production steps, and enhance resource utilization. This leads to cost savings and improved profitability.
Improved product quality and reliability: DFM engineers focus on eliminating potential manufacturing issues early in the design phase, resulting in products that are easier to produce consistently and with higher quality. This leads to improved customer satisfaction and brand reputation.
Accelerated time-to-market: By considering manufacturing constraints from the outset, DFM engineers streamline the production process, reducing the time required to bring a product to market. This gives companies a competitive edge and allows them to respond quickly to market demands.
Enhanced collaboration between design and manufacturing teams: DFM engineers act
between design and manufacturing teams, fostering effective communication and collaboration. By involving DFM engineers early in the design process, potential conflicts or challenges between the two teams can be resolved proactively, resulting in a more seamless and efficient product development cycle.
To illustrate the impact of Design-For-Manufacture engineering, let's consider a couple of case studies:
Example 1: Streamlining the production of a consumer electronics device
In this case, a Design-For-Manufacture engineer collaborated with the design team to optimize the manufacturing process of a new consumer electronics device. By analyzing the design specifications, the engineer identified opportunities to simplify the assembly process, reduce the number of components, and eliminate potential manufacturing bottlenecks. As a result, the production time was significantly reduced, leading to cost savings and a faster time-to-market for the product.
Reducing assembly time and costs for an automotive component
In this scenario, a DFM engineer worked closely with the manufacturing team to improve the production process of an automotive component. Through careful analysis of the design, the engineer suggested design modifications that simplified the assembly steps and reduced the number of required tools. This optimization not only reduced the assembly time but also minimized the risk of errors during the manufacturing process. As a result, the overall production costs were reduced, and the quality of the automotive component improved.
Challenges and Solutions
While Design-For-Manufacture engineering offers significant benefits, it is not without its challenges. Some common challenges include:
Overcoming design constraints without compromising functionality: DFM engineers need to balance design creativity with manufacturing constraints. They must find solutions that maintain the intended functionality of the product while ensuring its feasibility and cost-effectiveness in production. This requires collaboration and effective communication between design and manufacturing teams.
Balancing design creativity with manufacturing constraints: DFM engineers often face the challenge of finding innovative solutions that meet both design requirements and manufacturing constraints. By leveraging their technical expertise and collaborating closely with designers, they can explore alternative materials, manufacturing techniques, and assembly methods to achieve the desired outcome.
Addressing supply chain and logistical challenges: DFM engineers need to consider supply chain factors such as sourcing materials, coordinating with suppliers, and managing logistics. They must ensure that the necessary resources are available in a timely manner to support the manufacturing process and avoid potential disruptions.
To overcome these challenges, companies can invest in training and development programs for DFM engineers, encourage cross-functional collaboration, and leverage advanced technologies and tools that facilitate design optimization and manufacturing efficiency.
As technology continues to advance, Design-For-Manufacture engineering is poised to embrace several future trends:
Integration of artificial intelligence and machine learning: AI and machine learning algorithms can analyze vast amounts of data and provide valuable insights for design optimization. By leveraging these technologies, DFM engineers can enhance their decision-making processes, identify patterns, and predict potential manufacturing issues more accurately.
Adoption of advanced manufacturing technologies: With the rise of additive manufacturing, robotics, and automation, DFM engineers can leverage these technologies to further enhance the efficiency and precision of the production process. This includes 3D printing of prototypes, robotic assembly, and automated quality control systems.
Emphasis on sustainable and environmentally friendly practices: DFM engineering can play a crucial role in promoting sustainability in manufacturing. By considering the environmental impact of product design and manufacturing processes, DFM engineers can identify opportunities to reduce waste, minimize energy consumption, and incorporate eco-friendly materials.
and feasibility, ensuring that products can be manufactured efficiently without compromising quality or functionality. They analyze designs, optimize them for cost and efficiency, conduct feasibility studies, and create detailed manufacturing guidelines.
The benefits of Design-For-Manufacture engineering are substantial, including reduced production costs and waste, improved product quality and reliability, accelerated time-to-market, and enhanced collaboration between design and manufacturing teams. Real-world case studies demonstrate how DFM engineers have streamlined production processes and reduced costs for various products, such as consumer electronics devices and automotive components.
However, Design-For-Manufacture engineering also comes with its own set of challenges. DFM engineers must balance design constraints with functionality, finding innovative solutions that meet both requirements. They must also address supply chain and logistical challenges to ensure a smooth manufacturing process.
Looking ahead, the future of Design-For-Manufacture engineering holds exciting possibilities. Integration of artificial intelligence and machine learning will enable more accurate design optimization, while advanced manufacturing technologies like additive manufacturing and robotics will further enhance efficiency and precision. There will also be a growing emphasis on sustainable practices, with DFM engineers playing a crucial role in reducing waste and promoting eco-friendly manufacturing.
What is the primary goal of a Design-For-Manufacture Engineer?
The primary goal of a Design-For-Manufacture Engineer is to optimize product designs for efficient and cost-effective manufacturing processes without compromising quality or functionality.
How does Design-For-Manufacture Engineering impact product cost?
Design-For-Manufacture Engineering helps reduce production costs by optimizing designs for manufacturing efficiency, minimizing material waste, and streamlining production processes.
What software tools are commonly used by Design-For-Manufacture Engineers?
Design-For-Manufacture Engineers often utilize computer-aided design (CAD) software, simulation tools, and data analytics software to analyze designs, conduct feasibility studies, and optimize manufacturing processes.
Can Design-For-Manufacture Engineering be applied to any industry?
Yes, Design-For-Manufacture Engineering principles can be applied to various industries, including consumer electronics, automotive, aerospace, and many others. The goal is to ensure efficient and cost-effective manufacturing processes regardless of the industry.
How can companies integrate Design-For-Manufacture Engineering into their existing processes?
Companies can integrate Design-For-Manufacture Engineering by fostering collaboration between design and manufacturing teams, providing training and resources for DFM engineers, and adopting advanced technologies and tools that facilitate design optimization and manufacturing efficiency