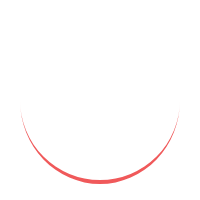
DIPLOMA IN BARE BOARD TESTING OPERATOR |
Bare board testing, also known as PCB testing or electrical testing, is the process of evaluating the integrity of a PCB before it undergoes component assembly. It involves checking the connectivity, continuity, and functionality of the conductive traces, vias, and pads on the board. The objective is to identify any defects, such as short circuits, open circuits, or incorrect routing, that could impact the performance or reliability of the final assembled product.
Bare board testing is a critical quality control measure in the PCB manufacturing industry. It helps to ensure that the bare boards meet the required standards and specifications before further production steps are undertaken. By detecting and addressing defects at an early stage, bare board testing minimizes the risk of faulty boards reaching the assembly stage, reducing costly rework or field failures.
Being a bare board testing operator requires a combination of technical skills, attention to detail, and problem-solving abilities. Some of the key skills and qualifications for this role include:
Knowledge of PCB Manufacturing: A thorough understanding of the PCB manufacturing process, including board fabrication, materials, and industry standards.
Electronic Testing Skills: Proficiency in using testing equipment such as digital multimeters, oscilloscopes, and boundary scan testers to perform electrical tests on PCBs.
Reading Schematics: Ability to interpret and understand schematic diagrams and design files to identify test points and verify connectivity.
Troubleshooting: Strong troubleshooting skills to diagnose and resolve issues encountered during testing, including identifying and isolating defects.
Attention to Detail: Meticulousness and a keen eye for detail to ensure accurate testing and identification of even the smallest defects.
Documentation and Reporting: Good record-keeping skills to document test results, generate reports, and communicate findings to relevant stakeholders.
Quality Control Knowledge: Familiarity with quality control processes and methodologies to ensure adherence to industry standards and specifications.
To become a competent bare board testing operator, individuals can pursue specialized training and certification programs. These programs provide in-depth knowledge of PCB testing techniques, equipment operation, and industry best practices. Some training programs may cover topics such as:
Fundamentals of PCB design and fabrication
Test point identification and probing techniques
Test method selection and optimization
Test program development and automation
Defect identification and troubleshooting
Certification programs validate the skills and knowledge of bare board testing operators, enhancing their employability and professional credibility within the industry.
The demand for skilled bare board testing operators is significant in the electronics manufacturing industry. Job opportunities can be found in PCB manufacturing companies, electronic contract manufacturing services (EMS) providers, and companies involved in the production of consumer electronics, automotive electronics, aerospace systems, and telecommunications equipment.
The salary of a bare board testing operator can vary based on factors such as location, experience, industry sector, and company size. Generally, entry-level positions offer a competitive salary, and as operators gain experience and expertise, they can progress to higher-paying roles such as test engineering or quality control.
Being a bare board testing operator comes with its own set of challenges and responsibilities. Some of these include:
Ensuring accurate and reliable test results within tight production schedules.
Identifying and resolving complex electrical issues and defects.
Adapting to new testing technologies and techniques as the industry evolves.
Collaborating with design engineers and manufacturing personnel to improve the testability and manufacturability of PCBs.
Maintaining a safe working environment and following proper electrostatic discharge (ESD) precautions.
Bare board testing operators utilize various tools and equipment to perform electrical tests on PCBs. Some commonly used tools include:
Digital Multimeters (DMM): Used to measure voltage, current, and resistance to verify the electrical integrity of circuits.
Boundary Scan Testers: Employed for testing and programming digital devices on the PCB using the IEEE 1149.x standard.
Oscilloscopes: Utilized to analyze and measure electronic signals and waveforms for troubleshooting and performance evaluation.
In-Circuit Testers (ICT): Specialized equipment used to test individual components and verify connectivity on assembled PCBs.
Functional Test Systems: Used to validate the overall functionality and performance of the PCB by simulating real-world operating conditions.
During bare board testing, operators often encounter a range of defects that can impact the performance and reliability of PCBs. Some common defects include:
Short Circuits: Unintended electrical connections between conductive traces or pads.
Open Circuits: Interruptions in the electrical pathways, resulting in discontinuity.
Incorrect Routing: Errors in the routing of traces that lead to connectivity issues or signal interference.
Insufficient Copper Thickness: Inadequate copper plating, leading to reduced conductivity or weak solder joints.
Solder Mask Defects: Imperfections in the protective solder mask layer, such as pinholes or misalignment.
To ensure effective and efficient bare board testing, operators should follow industry best practices. Some key best practices include:
Test Coverage Optimization: Prioritize critical nets and components to maximize test coverage and minimize test time.
Test Point Accessibility: Design PCBs with easily accessible test points to facilitate efficient probing during testing.
Test Program Validation: Validate test programs to ensure accurate and reliable test results before deployment.
Process Documentation: Maintain comprehensive documentation of test procedures, equipment calibration, and test setup to ensure repeatability.
Continuous Improvement: Regularly review and update testing processes based on feedback and lessons learned to enhance overall efficiency and yield.
The field of bare board testing is continually evolving, driven by advancements in technology and increasing demands for higher reliability and quality. Some notable industry trends include:
Automated Testing: Increasing adoption of automated test equipment (ATE) and test program automation to improve efficiency and reduce human errors.
Advanced Test Techniques: Emergence of new testing techniques, such as boundary scan testing, flying probe testing, and automated optical inspection (AOI), to detect complex defects and improve fault coverage.
IoT and Industry 4.0 Integration: Integration of bare board testing with IoT-enabled systems and Industry 4.0 concepts for enhanced connectivity, data analytics, and remote monitoring of test processes.
Miniaturization and High-Density Interconnects: The trend towards smaller form factors and high-density interconnects poses new challenges for bare board testing, requiring innovative test methodologies and equipment.
Q1. How long does it take to complete a diploma program in bare board testing?
A1. The duration of diploma programs in bare board testing can vary, but typically they range from a few months to a year, depending on the program and its curriculum.
Q2. Are there any specific certifications for bare board testing operators?
A2. Yes, several certification programs are available that validate the skills and knowledge of bare board testing operators. Some well-known certifications include IPC-A-600, IPC-6012, and J-STD-001.
Q3. What are the career prospects for bare board testing operators?
A3. The demand for skilled bare board testing operators is steady, and there are ample career opportunities in PCB manufacturing companies, EMS providers, and various industries that rely on electronics production.
Q4. Can I perform bare board testing manually without specialized equipment?
A4. While manual testing is possible for basic connectivity checks, specialized equipment such as digital multimeters and boundary scan testers are necessary for accurate and comprehensive testing.
Q5. How can I keep up with the latest advancements in bare board testing?
A5. Staying updated with industry publications, attending relevant conferences and seminars, and engaging in continuous learning and professional development can help you stay abreast of the latest advancements in bare board testing.
Bare board testing, also known as PCB testing or electrical testing, is the process of evaluating the integrity of a PCB before it undergoes component assembly. It involves checking the connectivity, continuity, and functionality of the conductive traces, vias, and pads on the board. The objective is to identify any defects, such as short circuits, open circuits, or incorrect routing, that could impact the performance or reliability of the final assembled product.