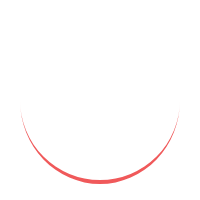
Assembly operators play a crucial role in the manufacturing industry, where efficiency and precision are paramount. They are responsible for assembling components, operating machinery, and ensuring the quality of the final products. In recent years, assembly operators have been working in collaboration with Programmable Logic Controllers (PLCs) to enhance productivity and streamline manufacturing processes. This article explores the significance of assembly operators in the context of PLCs, their responsibilities, required skills, and the future outlook for this profession.
Assembly operators are vital contributors to the manufacturing industry, playing a pivotal role in the production processes. Their primary responsibility is to assemble components, following specific guidelines and instructions. They work with various tools and equipment to complete tasks efficiently while maintaining high product quality standards.
Responsibilities of Assembly Operators
Assembly operators perform a range of tasks, including but not limited to:
Reading and interpreting assembly instructions and blueprints
Operating machinery and tools required for assembly
Ensuring accurate placement and alignment of components
Performing quality checks to identify defects or inconsistencies
Collaborating with team members to meet production targets
Maintaining a clean and organized workspace
Importance of Assembly Operators in Production Processes
Assembly operators are the backbone of manufacturing operations. Their precision and attention to detail ensure that products are assembled correctly, meeting the required specifications. By following standardized procedures, they contribute to consistent quality, reducing errors and minimizing rework. Assembly operators' work directly impacts the overall efficiency and productivity of the manufacturing process.
To optimize manufacturing operations, assembly operators have started using PLCs as a valuable tool. A Programmable Logic Controller is a digital computer system that controls industrial processes and machinery. It uses a programmable memory to store instructions and execute them based on specific conditions.
Definition and Functionality of PLCs
PLCs are designed to automate and control manufacturing processes. They can perform tasks such as monitoring inputs, making logical decisions, and activating outputs. These controllers are highly flexible and can be programmed to accommodate various production requirements. They offer real-time monitoring, diagnostics, and precise control, making them ideal for complex and high-speed manufacturing environments.
Applications of PLCs in Industrial Automation
PLCs find applications in a wide range of industries, including automotive, pharmaceuticals, food and beverage, and electronics. They are used in tasks such as:
Controlling assembly lines and conveyors
Managing robotic systems
Monitoring and adjusting temperature, pressure, and other variables
Implementing safety protocols and emergency shutdowns
By incorporating PLCs into their operations, assembly operators can enhance efficiency, improve product quality, and reduce human error.
The Collaboration between Assembly Operators and PLCs
Assembly operators have embraced PLCs as valuable tools to streamline their work and enhance productivity. The collaboration between assembly operators and PLCs brings numerous benefits to the manufacturing process.
How Assembly Operators Utilize PLCs in Manufacturing
Assembly operators utilize PLCs in various ways, such as:
Automating repetitive tasks: PLCs can perform tasks that would otherwise require significant manual effort, freeing up assembly operators to focus on more complex and value-added activities.
Ensuring precise control: PLCs allow assembly operators to program and control machinery with high precision, ensuring consistent quality and reducing errors.
Real-time monitoring: PLCs provide assembly operators with real-time data on machine performance, production rates, and quality parameters, enabling them to identify and address issues promptly.
Streamlining changeovers: With PLCs, assembly operators can reconfigure production lines quickly, minimizing downtime during changeovers and enabling efficient batch production.
Error detection and diagnostics: PLCs can detect errors or abnormalities in the manufacturing process, alerting assembly operators to take corrective actions promptly.
Benefits of Using PLCs for Assembly Operators
The utilization of PLCs offers several benefits to assembly operators:
Increased productivity: PLCs automate repetitive tasks, enabling assembly operators to focus on more complex aspects of their work, ultimately leading to higher productivity and throughput.
Enhanced quality control: With precise control over assembly processes, assembly operators can minimize defects and maintain consistent product quality.
Improved safety: PLCs can incorporate safety protocols and emergency shutdown systems, reducing the risk of accidents and injuries for assembly operators.
Data-driven decision making: PLCs provide real-time data on production parameters, enabling assembly operators to make data-driven decisions and optimize processes for better performance.
Skill development: By working with PLCs, assembly operators can acquire new technical skills and knowledge related to automation and control systems, enhancing their professional growth opportunities.
The collaboration between assembly operators and PLCs is a win-win situation, benefiting both the operators and the manufacturing industry as a whole.
To succeed as an assembly operator, individuals need to possess a combination of technical skills, communication abilities, and safety consciousness.
Technical Skills
Assembly operators must be proficient in:
Reading and interpreting technical drawings and assembly instructions
Operating hand tools, power tools, and machinery
Understanding and following quality control procedures
Troubleshooting basic mechanical issues
Basic knowledge of electrical systems and components
Communication and Collaboration Skills
Assembly operators often work in teams and need to effectively communicate with their colleagues and supervisors. Strong communication and collaboration skills ensure smooth coordination, enabling the assembly process to proceed efficiently.
Safety and Quality Assurance Skills
Assembly operators must prioritize safety and follow proper safety protocols to minimize the risk of accidents and injuries. Additionally, they should have a keen eye for detail and possess quality assurance skills to identify defects and inconsistencies in the assembly process.
Becoming an assembly operator typically requires a combination of vocational training and on-the-job experience. Various educational pathways can prepare individuals for a career as an assembly operator.
Vocational and Technical Programs
Vocational schools and technical institutes offer programs that focus on manufacturing processes, assembly techniques, and the use of machinery. These programs provide hands-on training, teaching students the practical skills required for assembly operations. Some programs also cover topics like blueprint reading, quality control, and safety protocols.
On-the-Job Training
Many assembly operators receive training directly on the job. They start as apprentices or assistants, working under experienced operators to gain practical knowledge and develop their skills. On-the-job training allows individuals to learn specific assembly processes and become familiar with the machinery and tools used in their industry.
While formal education is beneficial, hands-on experience and continuous learning are essential for assembly operators to excel in their roles.
Working in a PLC environment presents certain challenges for assembly operators, requiring them to adapt and develop new skills to overcome these hurdles.
Adaptability to Technological Advancements
PLCs and automation technologies continue to evolve rapidly. Assembly operators need to stay updated with the latest advancements, learn new programming languages, and acquire skills to effectively operate and troubleshoot PLC systems. Embracing change and maintaining a proactive approach to learning is crucial in this dynamic environment.
Troubleshooting and Problem-Solving Skills
As assembly operators work with PLCs, they may encounter technical issues or malfunctions. The ability to diagnose and troubleshoot problems efficiently is vital. Assembly operators need to develop problem-solving skills and be resourceful in finding solutions to maintain smooth operations.
Ensuring Productivity and Efficiency
While PLCs offer automation benefits, assembly operators must adapt their roles to optimize productivity and efficiency in a changing environment. They need to find the right balance between manual tasks and automated processes, ensuring that they contribute effectively to the manufacturing process and meet production targets.
The future of assembly operators is closely intertwined with the growth of automation and Industry 4.0. While there may be concerns about job displacement due to automation, the role of assembly operators is expected to evolve rather than disappear entirely.
Automation Trends in Manufacturing
Manufacturing industries are increasingly adopting automation technologies to enhance productivity, reduce costs, and improve quality. PLCs play a central role in this automation revolution. Assembly operators who embrace automation and develop complementary skills to work in conjunction with PLCs will continue to be in demand.
Evolving Roles of Assembly Operators
As assembly processes become more automated, the role of assembly operators will shift towards overseeing and optimizing the automated processes. They will focus on programming and configuring PLC systems, performing maintenance tasks, and continuously improving manufacturing efficiency. The expertise of assembly operators will be crucial in ensuring the successful implementation and operation of automated systems.
In conclusion, assembly operators are indispensable in the manufacturing industry, working alongside PLCs to optimize production processes. Their responsibilities range from assembling components to ensuring product quality. The collaboration between assembly operators and PLCs brings numerous benefits, including increased productivity, improved quality control, and enhanced safety. To succeed as assembly operators, individuals need a combination of technical skills, communication abilities, and safety consciousness. Challenges such as technological advancements and maintaining productivity in a PLC environment require adaptability and problem-solving skills. The future outlook for assembly operators is promising, with the ongoing automation trends creating new opportunities for skilled operators to contribute to the manufacturing industry's growth.
1. What is the role of assembly operators in the manufacturing industry?
Assembly operators are responsible for assembling components, operating machinery, and ensuring product quality in the manufacturing industry. They play a vital role in the production process, following assembly instructions, and collaborating with team members to meet production targets.
2. How do assembly operators utilize PLCs in their work?
Assembly operators utilize PLCs to automate tasks, ensure precise control over assembly processes, and monitor production parameters in real-time. PLCs assist assembly operators in achieving higher productivity, consistent quality, and efficient changeovers.
3. What qualifications are required to become an assembly operator?
To become an assembly operator, individuals typically need a combination of vocational training and on-the-job experience. Vocational programs focusing on manufacturing processes, assembly techniques, and machinery operation can provide the necessary skills. Strong technical skills, communication abilities, and a safety-conscious mindset are essential.
4. What are the challenges faced by assembly operators in a PLC environment?
Assembly operators in a PLC environment face challenges such as adapting to technological advancements, developing troubleshooting skills, and ensuring productivity and efficiency in a changing automated environment.
5. What is the future outlook for assembly operators and PLCs in manufacturing?
The future outlook for assembly operators and PLCs is promising. While automation trends continue to grow, the role of assembly operators will evolve rather than disappear entirely. Skilled operators who can complement automation technologies and optimize processes will continue to be in demand.