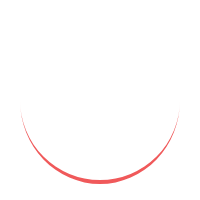
Here is some information on Diploma in Welding Technology
Diploma in Welding Technology is a Mechanical Engineering course. The course involves carbon steel, stainless steel, aluminum, etc. among the welding-type which are used are Shielded metal arc welding (SMAW), Gas Metal Arc Welding (GMAW), Gas Tungsten Arc Welding (GTAW), Submerge Arc Welding (SAW), etc. Through this course, the students will learn few things regarding quality assurance and control, inspection and testing, supervision, factory training, etc. the students will be equipped with computer software application skills. The training comprises planning skills, supervising the design, inspection and testing of the welding task to fulfill the quality assurance and safety rules.
Diploma in Welding Technology is a program that provides students with knowledge and skills in welding processes and techniques. This program aims to train students to become proficient in welding and joinery techniques for various metals and alloys, including steel, aluminum, and copper. The course also covers safety practices, welding inspection, and welding design.
Stream | Engineering |
Course | Diploma In Welding Technology |
Full Name | Diploma In Welding Technology |
Eligibility | 10th |
Duration | 1 Year |
Fees | 10000 |
Type | Diploma |
Mode | Year |
Applicants should have completed their 10+2 education with a minimum of 50% marks in science stream from a recognized board. Some institutes also offer the course to individuals with ITI certification in welding.
The students should have passed a 10+2 pass or its equivalent pass with Physics, Chemistry, Biology and Mathematics
The duration of the program is typically two years, but it may vary by institution.
Selection criteria may vary by institution but may include academic performance, relevant work experience, and personal interviews.
Institutions may assess applicants' technical aptitude
through various means, such as entrance exams, aptitude tests, or interviews. This helps determine the applicants' understanding of basic mathematics, physics, and mechanical concepts, which are essential for success in welding technology.
Hands-on Skills: Applicants with prior hands-on experience in welding or related fields may have an advantage during the selection process. Institutions may consider factors such as work experience, internships, or participation in vocational programs or workshops.
Interest and Motivation: Institutions may assess applicants' interest and motivation in pursuing a career in welding technology. This can be demonstrated through personal statements, letters of intent, or interviews where applicants articulate their passion for welding and their career goals in the field.
Some institutions may require applicants to take an entrance exam to assess their skills and knowledge in basic subjects like math, reading, and writing.
Interested individuals can apply to institutes offering Diploma in Welding Technology through their respective admissions departments.
Applicants are typically required to have completed a certain level of education, such as:
High school diploma or equivalent (e.g., GED)
Secondary school certificate
Vocational training certificate in a related field
The application form and process may vary by institution but typically involves filling out an application form, submitting academic transcripts, and paying an application fee.
The cost of Diploma in Welding Technology varies by institution and location. Students may be eligible for financial aid or scholarships.
The syllabus for Diploma in Welding Technology varies by institution but typically includes courses in welding processes, welding metallurgy, welding inspection, welding design, and safety practices.
Introduction to Welding Technology:
Overview of welding and its importance in various industries
Historical development of welding processes
Role of welding in manufacturing, construction, and repair industries
Welding Safety and Health:
Occupational safety regulations and practices in welding
Personal protective equipment (PPE) and its importance in welding
Hazard identification, risk assessment, and mitigation strategies in welding environments
Welding Metallurgy:
Fundamentals of metallurgy and materials science
Properties of metals and alloys relevant to welding
Effects of heat, pressure, and welding processes on material properties
Welding Processes:
Overview of common welding processes, including:
Shielded Metal Arc Welding (SMAW)
Gas Metal Arc Welding (GMAW)
Gas Tungsten Arc Welding (GTAW)
Flux-Cored Arc Welding (FCAW)
Submerged Arc Welding (SAW)
Principles, advantages, and limitations of each welding process
According to the U.S. Bureau of Labor Statistics, the median annual wage for welders, cutters, solderers, and brazers was $44,190 as of May 2020. Welders can find employment in the construction, manufacturing, and repair industries, working for companies or as self-employed individuals.
Salary Range: In the United States, welders typically earn between $30,000 and $60,000 per year, depending on factors such as experience, skills, industry, and geographical location.
Salary Range: Welding inspectors can earn salaries ranging from $50,000 to $100,000 per year, depending on experience, certifications (e.g., Certified Welding Inspector - CWI),
Salary Range: Welding supervisors or foremen typically earn salaries ranging from $50,000 to $90,000 per year, depending on experience, leadership skills, industry, and geographic location.
Welders can specialize in various areas of welding, such as structural welding, pipe welding, or aerospace welding. With experience and additional training, welders can advance to supervisory positions or become welding inspectors, welding engineers, or welding educators.
Welders are responsible for joining metal parts using various welding processes and techniques. They work in industries such as manufacturing, construction, automotive, aerospace, and shipbuilding.
Welding inspectors ensure that welding work meets quality standards, codes, and specifications. They inspect welds visually and using non-destructive testing (NDT) methods to detect defects and ensure structural integrity.
Welding supervisors or foremen oversee welding projects, manage welding teams, and ensure that work is completed safely, efficiently, and according to specifications. They coordinate with clients, engineers, and other stakeholders to plan and execute welding operations.