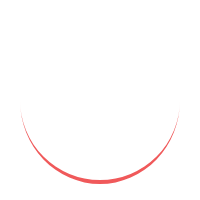
Tungsten Inert Gas (TIG) welding is a versatile and widely used welding process known for its precision and high-quality welds. TIG welding Level 5 represents a higher level of expertise and skill within the TIG welding domain. In this article, we will explore the various aspects of TIG welding Level 5, including its benefits, applications, key features to consider when choosing a TIG welder, safety precautions, maintenance tips, troubleshooting common issues, and more.
Introduction to Tungsten Inert Gas (TIG) Welding
TIG welding is a welding technique that uses a non-consumable tungsten electrode to create the weld. The inert gas, typically argon, is used to shield the welding area from atmospheric contamination. This process allows for precise control over the welding arc, resulting in high-quality welds with minimal splatter or spatter.
Understanding TIG Welding Level 5
TIG welding Level 5 is the highest level of proficiency in TIG welding. It requires a deep understanding of welding principles, advanced techniques, and the ability to produce exceptional welds in various materials and positions. Level 5 welders have honed their skills through extensive training and hands-on experience, making them capable of tackling complex welding projects with precision and efficiency.
Benefits of TIG Welding Level 5
TIG welding Level 5 offers numerous benefits over other welding processes. Firstly, it provides superior control over the welding arc, resulting in precise and aesthetically pleasing welds. The process also allows for welding a wide range of materials, including stainless steel, aluminum, copper, and titanium, making it suitable for diverse applications. Additionally, TIG welding Level 5 produces welds with excellent mechanical properties, such as high strength and corrosion resistance.
Applications of TIG Welding Level 5
TIG welding Level 5 finds applications in various industries, including aerospace, automotive, construction, and manufacturing. It is commonly used for welding critical components, such as aircraft parts, pressure vessels, pipelines, and precision instruments. The ability to weld different materials and produce clean, high-quality welds makes TIG welding Level 5 indispensable in industries where aesthetics and structural integrity are paramount.
Choosing the Right TIG Welder Level 5
When selecting a TIG welder Level 5, there are several factors to consider. Firstly, ensure that the welder offers the necessary amperage range and duty cycle to handle the types of projects you intend to undertake. Look for welders with advanced features like pulse welding, adjustable waveforms, and high-frequency starting, as these can enhance your welding capabilities. Additionally, consider the portability, ease of use, and reliability of the welder.
Key Features to Consider in TIG Welders Level 5
When investing in a TIG welder Level 5, it's crucial to pay attention to certain key features. Look for a welder with precise amperage control and the ability to adjust pulse settings, as these can greatly enhance weld quality. An intuitive interface, clear display, and user-friendly controls contribute to a smoother welding experience. Also, consider the availability of essential accessories such as foot pedals, torches, and gas regulators.
Safety Precautions for TIG Welding Level 5
Safety should always be a top priority when engaging in TIG welding Level 5. Ensure proper ventilation in the welding area to prevent the accumulation of hazardous fumes. Wear protective gear, including welding helmets with auto-darkening filters, heat-resistant gloves, and flame-resistant clothing. Adhere to electrical safety guidelines and inspect all equipment regularly for any signs of damage or malfunction.
Tips for Successful TIG Welding Level 5
To achieve successful TIG welds at Level 5, there are several tips and techniques to keep in mind. Maintain a stable hand and precise control of the torch movement. Properly prepare the weld joint by cleaning and removing any contaminants. Use the correct filler material and adjust the welding parameters based on the material thickness. Practice and develop a steady welding technique to ensure consistent and high-quality welds.
Maintenance and Care of TIG Welders Level 5
Regular maintenance and care are essential for prolonging the lifespan of TIG welders Level 5. Keep the welding equipment clean and free from debris or dust. Inspect the torch, electrode, and gas nozzles for signs of wear and replace them as necessary. Perform routine checks on the power supply, cables, and gas lines to ensure proper functioning. Regularly calibrate and adjust the welder's settings to maintain accuracy.
Troubleshooting Common Issues in TIG Welding Level 5
Even experienced welders may encounter common issues during TIG welding Level 5. Some common problems include tungsten contamination, insufficient gas coverage, porosity, and improper fusion. Understanding the root causes of these issues and implementing appropriate corrective measures can help achieve consistent weld quality. Proper tungsten preparation, gas flow rate adjustment, and controlling the welding parameters are crucial in troubleshooting and resolving these issues.
Training and Certification for TIG Welding Level 5
To reach TIG welding Level 5, comprehensive training and certification programs are available. These programs provide a structured curriculum that covers theoretical knowledge, practical skills, and hands-on experience. Completing these programs and obtaining relevant certifications demonstrate a welder's proficiency and expertise in TIG welding Level 5. Continuous learning and staying updated with industry advancements further enhance a welder's capabilities.
Future Trends in TIG Welding Level 5
The field of TIG welding Level 5 continues to evolve, driven by advancements in technology and industry requirements. Future trends include the integration of automation and robotics in TIG welding processes to improve efficiency and productivity. Innovations in filler materials, shielding gases, and welding consumables aim to enhance weld quality and expand the range of materials that can be welded using TIG processes.
Environmental Considerations in TIG Welding Level 5
Environmental considerations are becoming increasingly important in welding processes, including TIG welding Level 5. Opting for environmentally friendly shielding gases and reducing the use of hazardous chemicals and consumables can minimize the impact on the environment. Proper waste management, recycling, and adherence to regulations and guidelines ensure responsible and sustainable TIG welding practices.
Cost Analysis of TIG Welding Level 5
The cost associated with TIG welding Level 5 includes the initial investment in the welder and associated equipment, ongoing maintenance and consumable expenses, and training and certification costs. However, the high-quality welds and versatility offered by TIG welding Level 5 often justify the investment, especially in industries where precision and aesthetics are critical.
FAQs
Q1: Is TIG welding Level 5 suitable for beginners?
A1: TIG welding Level 5 requires advanced skills and expertise, making it more suitable for experienced welders. Beginners should start with basic TIG welding techniques and gradually progress to higher levels.
Q2: Can TIG welding Level 5 be used for stainless steel welding?
A2: Yes, TIG welding Level 5 is particularly well-suited for stainless steel welding. It provides excellent control over the welding arc, resulting in clean and precise welds on stainless steel.
Q3: How long does it take to become proficient in TIG welding Level 5?
A3: Becoming proficient in TIG welding Level 5 requires extensive training, practice, and hands-on experience. The time required may vary depending on individual aptitude and dedication.
Q4: Can TIG welding Level 5 be automated?
A4: Yes, automation and robotics are increasingly being integrated into TIG welding processes, including Level 5. Automation offers advantages such as increased productivity, consistency, and reduced human error.
Q5: Are there any health risks associated with TIG welding Level 5?
A5: TIG welding Level 5, like any welding process, involves potential health risks. Welders should take necessary safety precautions, such as using proper ventilation, wearing protective gear, and minimizing exposure to welding fumes and UV radiation.