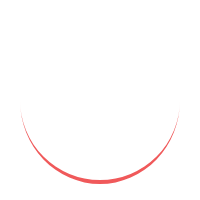
Resistance spot welding is a widely used method for joining metal parts in various industries such as automotive, aerospace, and construction. This technique involves the application of heat generated by electrical resistance to create a weld between two or more metal surfaces. To carry out this process effectively, skilled resistance spot welding machine operators are essential. In this article, we will explore the responsibilities, skills, training, work environment, challenges, and career opportunities associated with being a resistance spot welding machine operator.
Introduction to Resistance Spot Welding
Resistance spot welding is a type of electric welding that uses the resistance of materials to generate heat, creating a localized weld between metal surfaces. It involves clamping two or more metal pieces together and passing an electric current through them to create a weld at the point of contact. This process is commonly used in the manufacturing of automobiles, appliances, and other metal structures, as it provides a strong and efficient bond.
Importance of Resistance Spot Welding Machine Operators
Resistance spot welding machine operators play a crucial role in the production process, ensuring the proper functioning of welding equipment and the production of high-quality welds. They are responsible for setting up and operating the welding machines, monitoring the welding process, and inspecting the welds for quality. The skills and expertise of these operators directly impact the structural integrity and overall quality of the welded components.
Responsibilities of a Resistance Spot Welding Machine Operator
As a resistance spot welding machine operator, you will have various responsibilities to ensure efficient and accurate welding operations. Some of the key responsibilities include:
Machine Setup: Setting up the welding machine by adjusting parameters such as current, voltage, and timing according to the specifications provided.
Material Preparation: Preparing the metal surfaces to be welded by cleaning, removing contaminants, and aligning the parts correctly.
Machine Operation: Operating the welding machine, triggering the welding cycle, and monitoring the process for any abnormalities or deviations.
Quality Control: Inspecting the welds visually and using testing methods to ensure they meet the required specifications and quality standards.
Troubleshooting: Identifying and resolving any welding defects, machine malfunctions, or process issues that may affect the weld quality.
Documentation: Maintaining accurate records of welding parameters, inspection results, and any necessary documentation for traceability and quality assurance.
Essential Skills and Qualifications
To excel as a resistance spot welding machine operator, certain skills and qualifications are essential. These include:
Knowledge of Welding Principles and Techniques
A strong understanding of welding principles, including heat control, electrode selection, and weld joint design, is vital for a welding machine operator. Knowledge of different welding techniques, such as spot welding, seam welding, and projection welding, allows for effective operation and troubleshooting.
Understanding of Machine Operation
A resistance spot welding machine operator should have a thorough understanding of how the welding equipment functions. This includes knowledge of machine controls, adjustment mechanisms, and safety features. Being able to interpret machine readouts and indicators is crucial for monitoring and maintaining the welding process.
Ability to Read and Interpret Blueprints
Interpreting blueprints and technical drawings is necessary for accurately positioning and aligning the metal parts to be welded. Understanding welding symbols and specifications helps ensure compliance with design requirements and dimensional tolerances.
Attention to Detail and Quality Control
Attention to detail is critical in welding operations, as even minor deviations can affect the quality and integrity of the welds. A resistance spot welding machine operator must be meticulous in inspecting welds, identifying defects, and implementing corrective actions to maintain high-quality standards.
Safety Awareness and Compliance
Working with welding equipment involves inherent risks, including exposure to high temperatures, electrical hazards, and fumes. An operator should prioritize safety by following proper safety protocols, wearing personal protective equipment (PPE), and being aware of potential hazards associated with the welding process.
Training and Certification
Becoming a skilled resistance spot welding machine operator often requires a combination of formal training programs, on-the-job training, and certification.
Formal Training Programs
Many technical schools, community colleges, and vocational institutes offer welding programs that cover various welding techniques, including resistance spot welding. These programs provide a comprehensive understanding of welding principles, machine operation, blueprint reading, and safety practices.
On-the-Job Training
After completing formal training, on-the-job training is typically provided to familiarize operators with specific welding machines, production processes, and quality standards. This hands-on experience allows operators to refine their skills and gain practical knowledge in a real-world manufacturing environment.
Certification and Credentials
Obtaining industry-recognized certifications, such as those offered by the American Welding Society (AWS), can enhance job prospects and demonstrate proficiency as a resistance spot welding machine operator. These certifications typically involve written exams and practical assessments to validate the operator's knowledge and skills.
Work Environment and Conditions
Resistance spot welding machine operators work in a variety of manufacturing settings, such as automotive assembly plants, metal fabrication shops, and appliance manufacturing facilities. The work environment can vary but generally involves the following aspects:
Equipment and Tools
Operators utilize various types of welding machines, including manual, semi-automatic, and fully automated systems. They also work with a range of tools such as clamps, electrodes, weld fixtures, and measurement instruments.
Physical Demands
The job of a resistance spot welding machine operator can be physically demanding. It may involve standing for long periods, lifting and manipulating heavy metal parts, and maintaining proper body positioning during welding operations.
Safety Precautions
Adhering to safety precautions is paramount in welding operations. Operators must wear appropriate protective clothing, such as welding helmets, gloves, safety glasses, and fire-resistant attire. They should also be familiar with safety procedures, emergency protocols, and the safe handling of welding equipment.
Common Challenges and Troubleshooting
While operating resistance spot welding machines, operators may encounter various challenges and need to troubleshoot issues that can affect the welding process and the quality of the welds.
Welding Defects and Quality Issues
Welding defects, such as porosity, cracks, and incomplete fusion, can occur due to improper machine setup, inadequate cleaning of metal surfaces, or incorrect welding parameters. Operators must be able to identify these defects and implement corrective measures to ensure high-quality welds.
Machine Malfunctions and Maintenance
Welding machines may experience malfunctions or breakdowns, resulting in interruptions to the production process. Operators should have basic knowledge of machine maintenance and troubleshooting techniques to address minor issues and perform routine maintenance tasks.
Safety Hazards and Precautions
Working with welding equipment involves inherent safety hazards, including electrical shocks, burns, and exposure to harmful fumes and UV radiation. Operators must be vigilant about safety precautions, follow established safety protocols, and be trained in emergency response procedures.
Resistance Spot Welding Machine Operator Career Opportunities and Growth
The demand for skilled resistance spot welding machine operators remains steady in industries that rely on metal fabrication and assembly processes. As an operator gains experience and expertise, various career opportunities and avenues for growth become available.
Job Outlook and Demand
The manufacturing sector, particularly the automotive industry, continues to rely on resistance spot welding for the production of vehicles and components. This sustains the demand for qualified welding machine operators who can ensure efficient and accurate welding operations.
Advancement Opportunities
With experience, operators can advance to supervisory roles, such as welding team lead or production supervisor. They may also specialize in specific welding processes or become welding inspectors, quality control technicians, or welding engineers.
Continuing Education and Skill Development
To stay competitive and enhance career prospects, resistance spot welding machine operators should pursue continuing education and skill development opportunities. This can include attending workshops, seminars, or advanced training programs to learn about new welding technologies, emerging industry standards, and advanced welding techniques.
Q1: What is the role of a resistance spot welding machine operator?
A1: A resistance spot welding machine operator is responsible for setting up and operating welding machines, monitoring the welding process, inspecting weld quality, troubleshooting issues, and ensuring compliance with safety and quality standards.
Q2: How long does it take to become a certified welding machine operator?
A2: The duration to become a certified welding machine operator can vary. It generally involves completing a formal training program, which can range from a few months to a year, followed by on-the-job training. Certification exams may be taken after acquiring the necessary experience.
Q3: What are the common welding defects that a machine operator should be aware of?
A3: Common welding defects include porosity, cracks, incomplete fusion, and excessive spatter. These defects can arise from factors such as improper machine setup, inadequate cleaning of surfaces, or incorrect welding parameters.
Q4: Are there any specific safety measures for resistance spot welding?
A4: Yes, safety measures for resistance spot welding include wearing appropriate personal protective equipment (PPE), such as helmets, gloves, and safety glasses, following established safety protocols, and being aware of electrical hazards, fumes, and UV radiation.
Q5: Can a resistance spot welding machine operator work in different industries?
A5: Yes, resistance spot welding machine operators can find employment opportunities in various industries, including automotive, aerospace, appliance manufacturing, and metal fabrication, where metal joining is required.